Precision Liquid Silicone Rubber Injection Molding and Customized Solutions
Advanced Liquid Silicone Rubber Overmolding Technology for High-Precision Molding
Customized Silicone Components for the Medical Industry
Tailored Solutions for Medical Device Accessories
Tailored Solutions for Medical, Automotive, and Consumer Industries
For LSR Injection Molding & Plastic Injection Molding
50+ Sets of LSR Machines for High-Precision Production
5,000 m² Medical-Grade Cleanroom Facilities
Our Core Services | Leading LSR Injection Molding Expertise
Our state-of-the-art LSR injection molding facility features a Class 100K cleanroom and advanced process controls for exceptional consistency. We specialize in:
- Multi-material LSR injection molding technology
- Automated production cells for high-volume manufacturing
- Specialized solutions for medical, automotive and electronics industries.
Our precision plastic injection molding capabilities complement our LSR expertise, offering:
- Multi-cavity molds for high-volume efficiency
- Advanced material options including PC, PA, PBT, and custom compounds
- Insert molding and hybrid molding technologies
Our expert team specializes in custom mold design and manufacturing, delivering optimal solutions for complex injection molding requirements. We provide:
- Rapid tooling capabilities for quick market launch
- Professional material selection and process parameter optimization
- Precision mold manufacturing with high-accuracy machining
- Systematic mold testing and validation procedures
Our comprehensive post-processing capabilities ensure your products reach the highest quality standards from production to delivery. We offer:
- Advanced surface treatment solutions
- Customized laser marking and printing for product identification
- Rigorous quality inspection
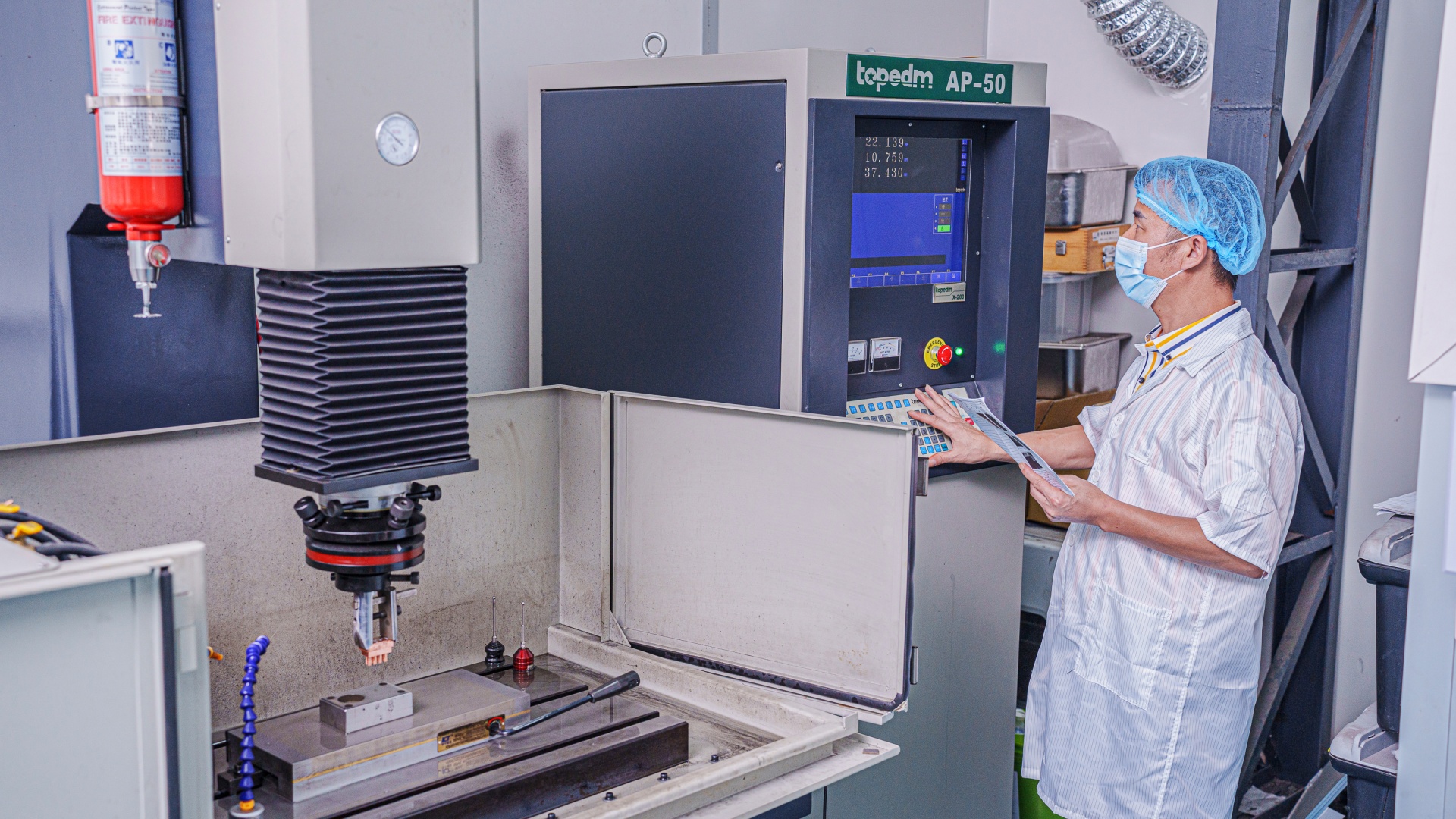
Liquid Silicone Rubber (LSR) Injection Molding
High-precision LSR molding for medical devices, automotive components, 3C electronics, and consumer goods.
ISO 13485 & ISO 9001 certified, ensuring top-quality manufacturing.
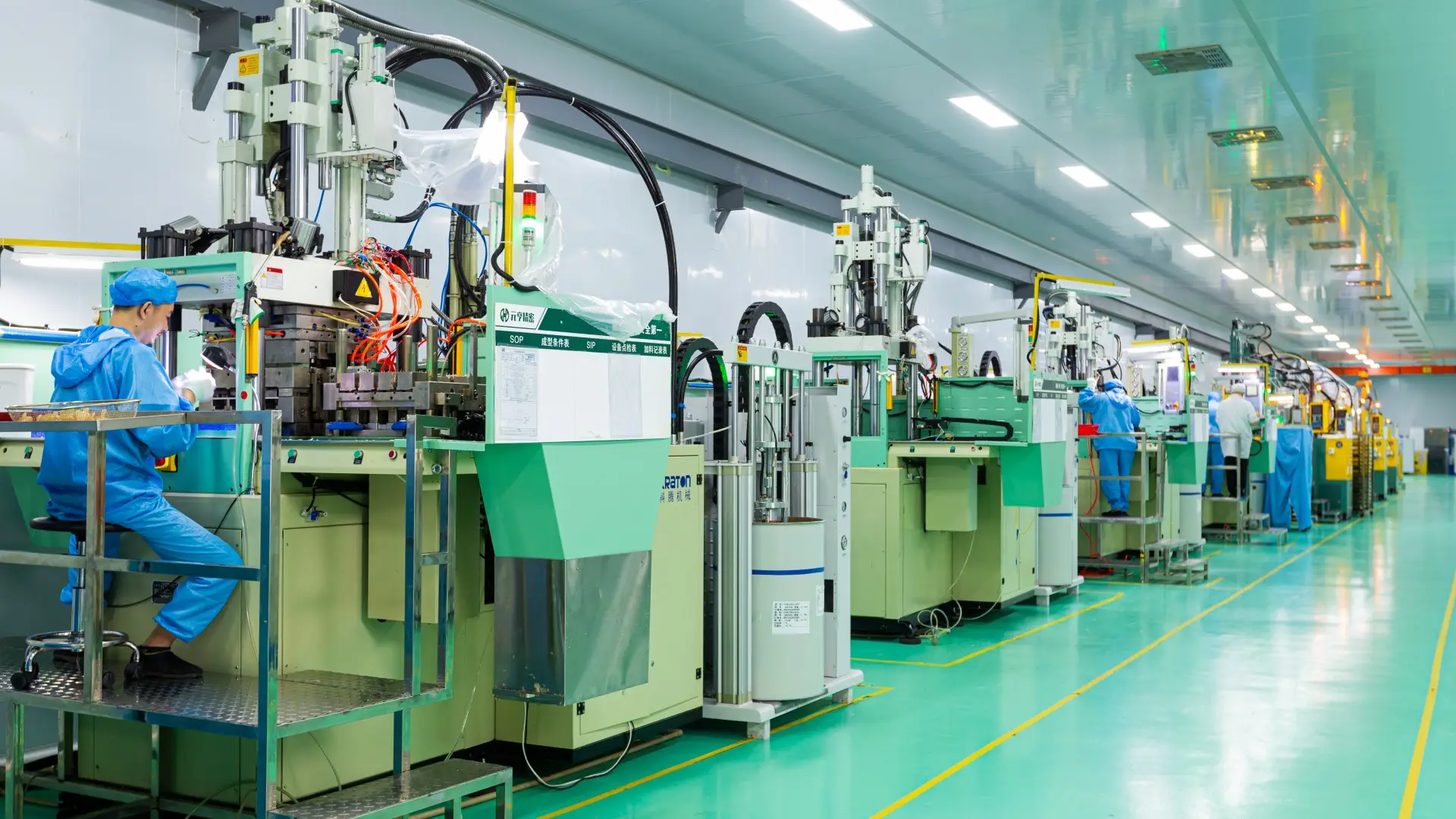
Overmolding & Multi-Material Injection
Advanced LSR overmolding technology for seamless integration with plastics, metals, and other substrates.
Perfect for medical wearables, automotive seals, and high-end electronics.
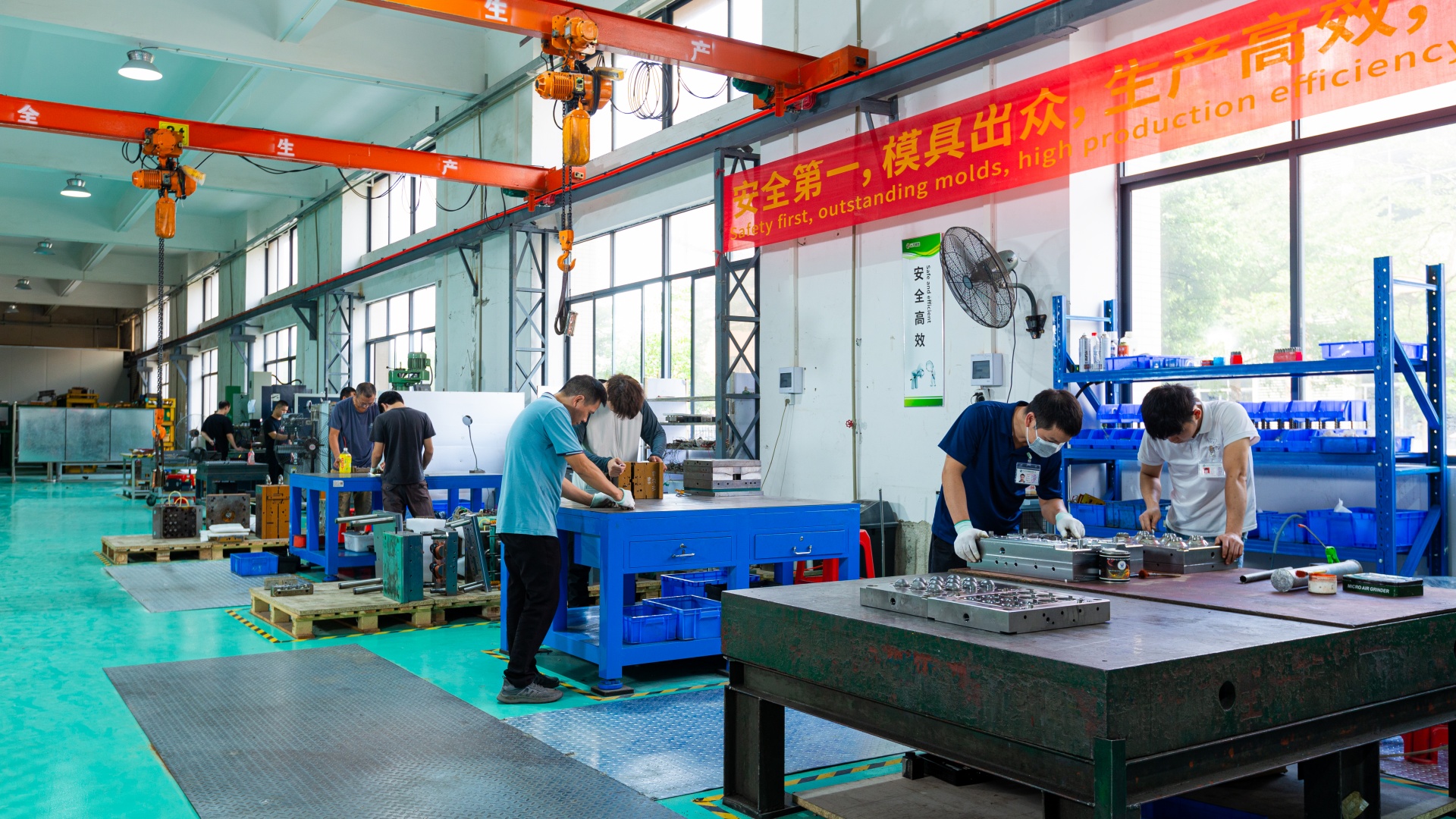
Precision Plastic Molding
High-performance thermoplastic injection molding for custom applications.
Servicing automotive, medical, and industrial sectors.
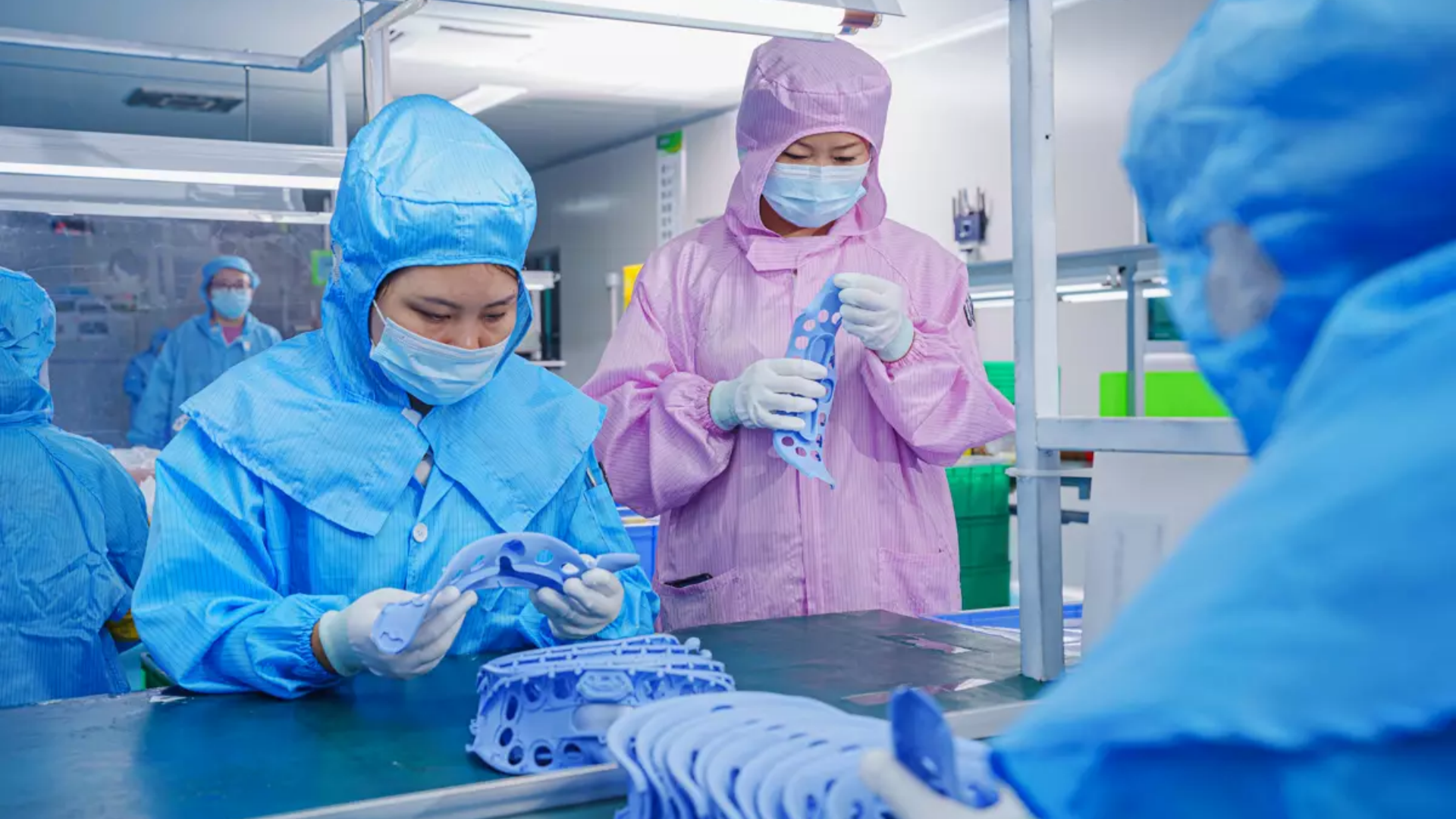
Post-Processing & Custom Finishing
Surface treatment, laser engraving, color matching, and pad printing available for custom branding.
Industries We Serve
Henry Precision Silicone Products Applications
Established in 2015, Henry Precision is a leading manufacturer specializing in liquid silicone rubber (LSR) injection molding and precision plastic mold production.
Based in Zhongshan City, China, we operate state-of-the-art Class 100K cleanrooms, utilize over 60 advanced injection molding machines, and achieve a monthly production capacity of 100 million+ units.
As a trusted silicone mold manufacturer and supplier, we deliver premium-quality, cost-effective silicone products for medical devices, automotive components, consumer electronics, and industrial applications, backed by ISO13485 and ISO9001-certified management systems.
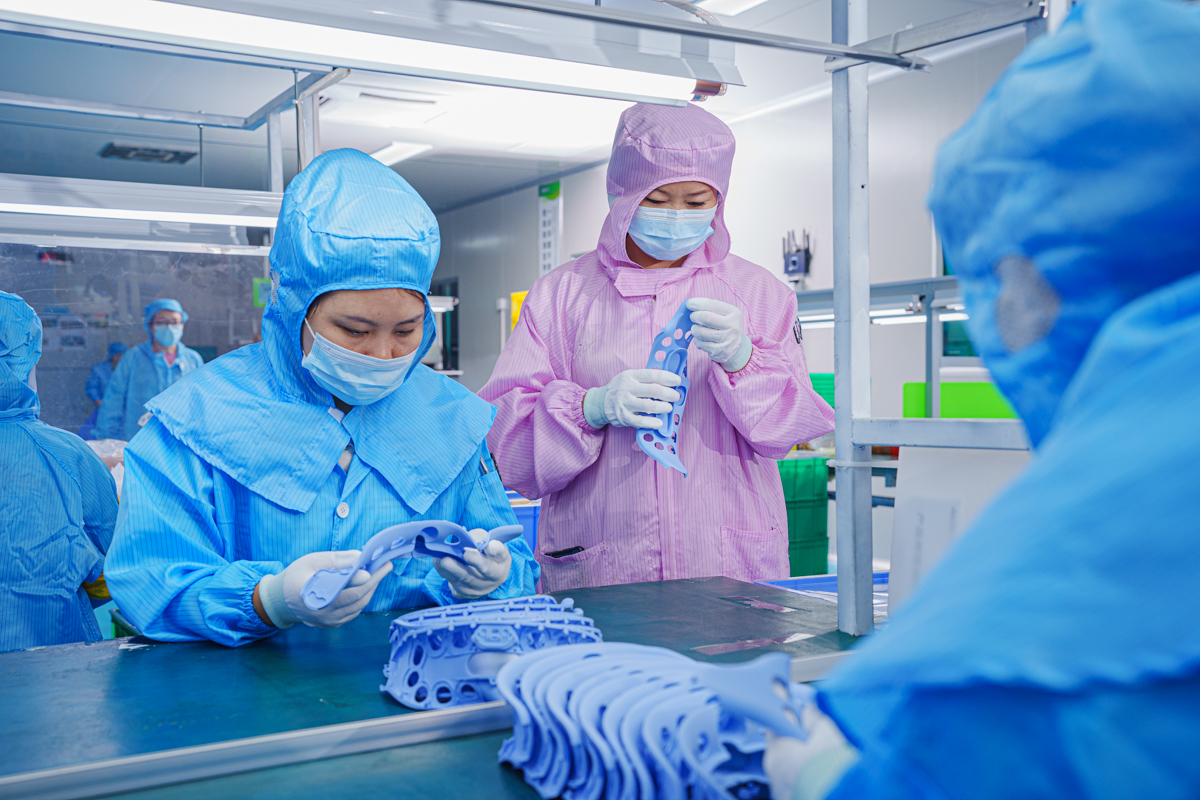
Automotive & Vehicles
Henry’s precision-molded silicone components are engineered for exceptional NVH (Noise, Vibration, Harshness) performance, ensuring optimal durability and reliability in electric vehicles (EVs), automotive sealing systems, and thermal management applications.
Medical
Our advanced silicone manufacturing capabilities, combined with ISO 13485-certified processes, deliver exceptional biocompatibility, precision, and durability.
3C Digital Electronics
We adopt the low Volatile Organic Compounds LSR materials to manufacture silicone parts for electronics. Dedicated to exploring the potential of LSR materials and molding technologies to enhance the durability and lifespan of 3C products.
Audio Device
For audio applications, we manufacture silicone mold products that deliver superior sound quality and durability for high-end audio products. All products undergo rigorous testing and quality control.
High-End Bathroom Products
With advanced surface treatment technologies and silicone molding capabilities, we achieve premium tactile feel and aesthetic finishes while ensuring reliable sealing performance under varying pressure and temperature conditions.
Henry Precision Silicone Products Applications

HealthCare
LSR transforms 3C digital products through innovation. As an experienced silicone mold maker, we specialize in speaker housings and airtight seals for electronics with superior waterproofing, dustproofing, and shock resistance. Silicone rubber suppliers trust our expertise for cutting-edge electronic solutions.
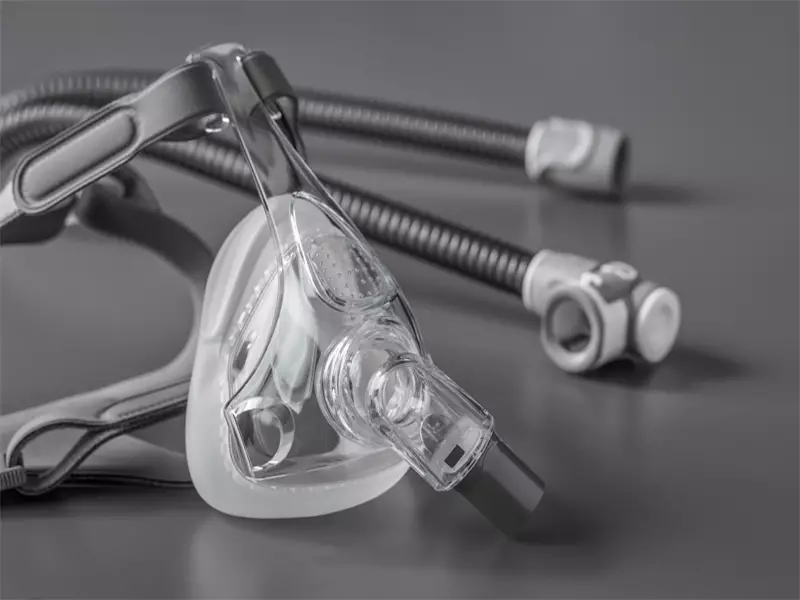

Smart Hardware & Consumer Electronics
LSR transforms 3C digital products through innovation. As an experienced silicone mold maker, we specialize in speaker housings and airtight seals for electronics with superior waterproofing, dustproofing, and shock resistance. Silicone rubber suppliers trust our expertise for cutting-edge electronic solutions.
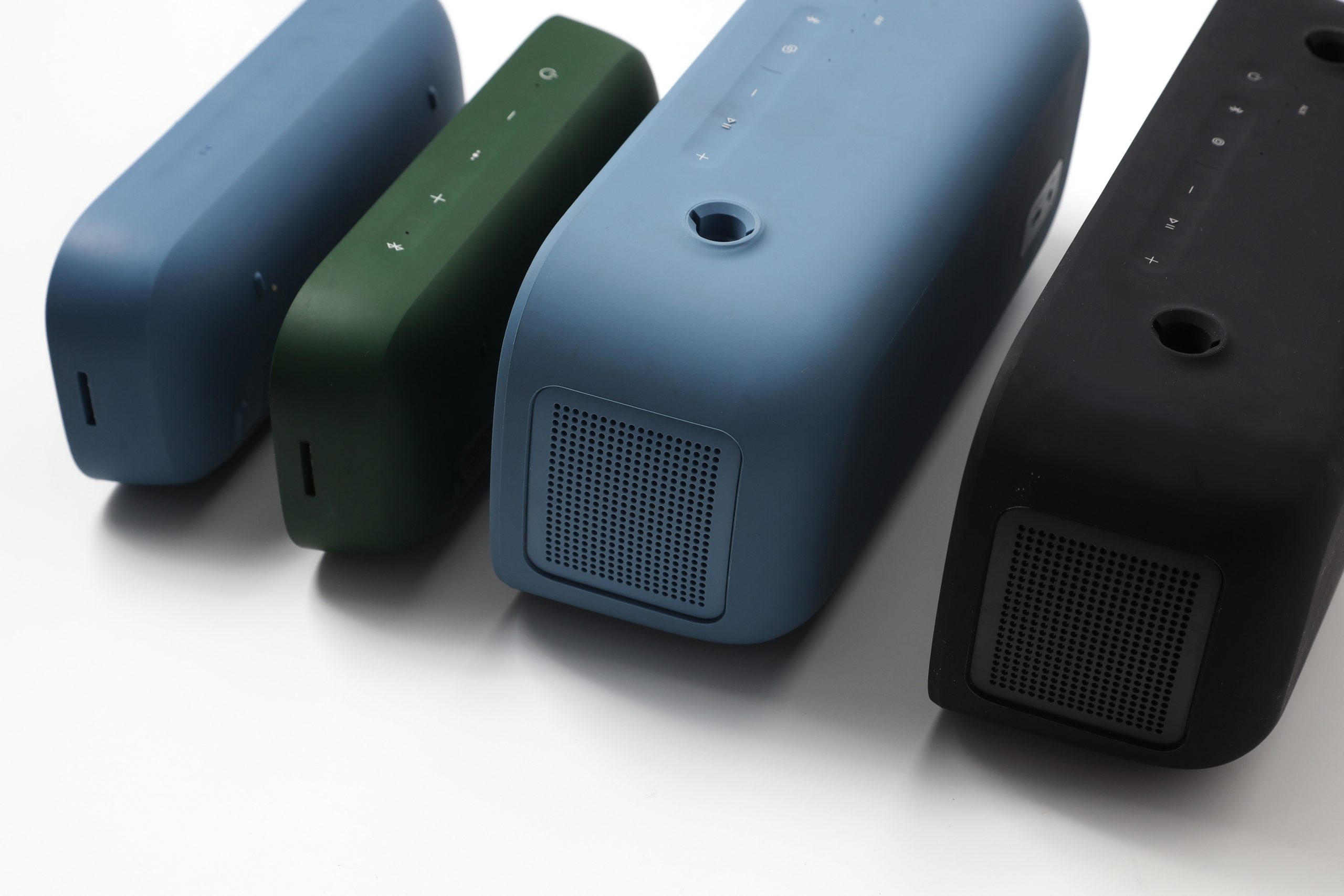

High-End Sanitary Goods
LSR is extensively used in premium sanitary ware and consumer goods, including seals, waterproof strips, and dustproof components. We enhance products through custom silicone molding and precision engineering, delivering outstanding durability, UV resistance, and aesthetic design.
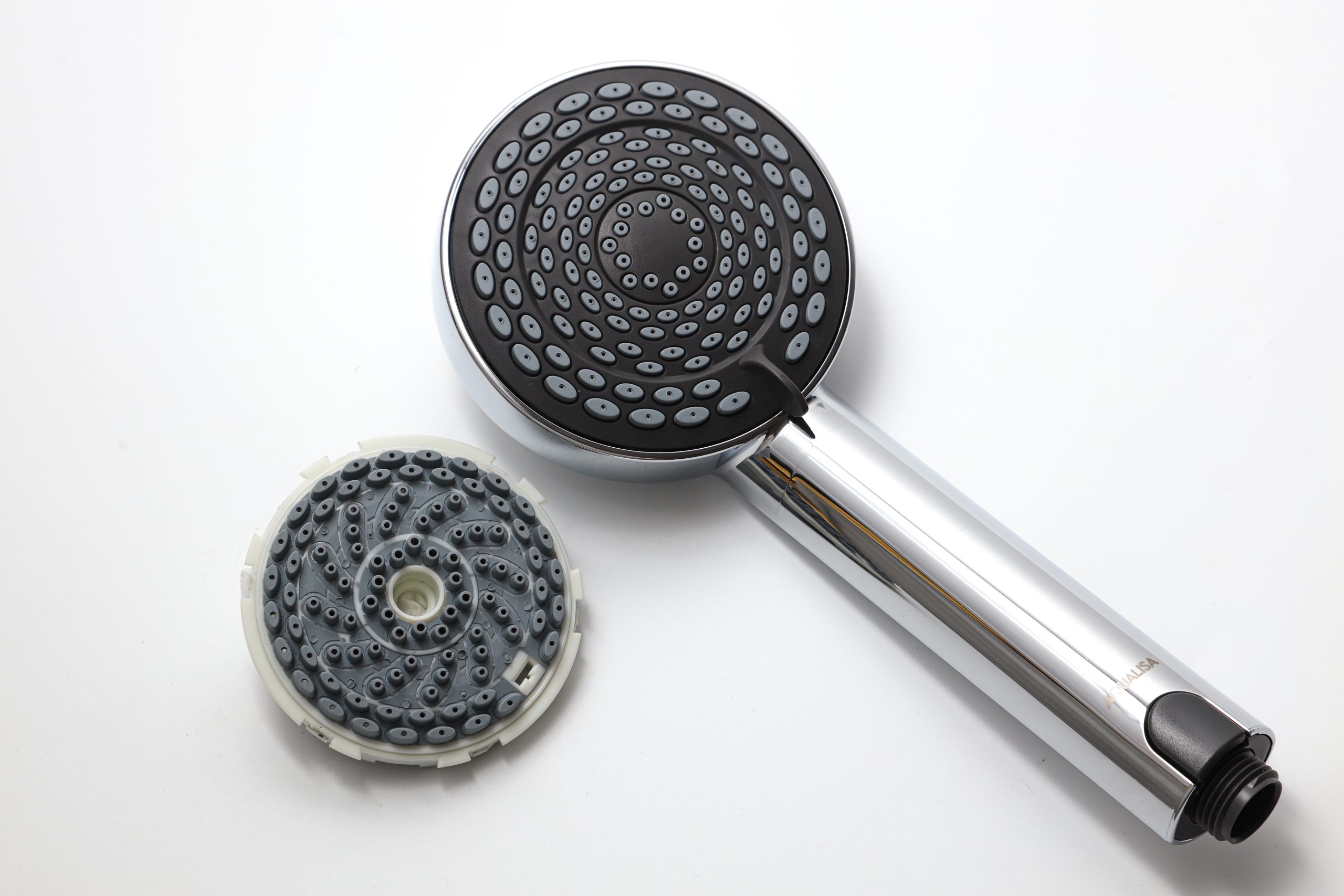

High-Performance Automotive Parts
LSR innovation drives automotive components like seals, gaskets, and connectors. With excellent resistance to high temperatures, UV exposure, and chemical corrosion, it ensures performance and reliability in demanding environments. Partner with our silicone manufacturing experts for superior automotive solutions.
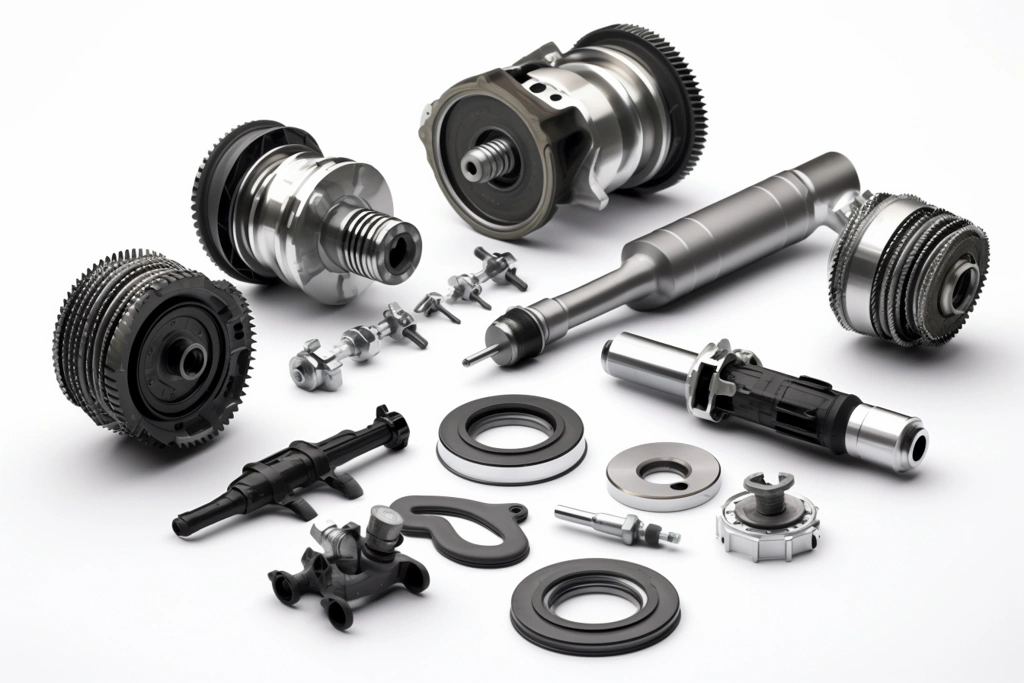
About Us
Founded in 2011, we specialize in Liquid Silicone Rubber (LSR) injection molding, offering customized solutions for industries such as medical devices, automotive, consumer electronics, and high-end bathroom products.
Our facility, spanning over 15,000 square meters with a 5,000 square meter Class 100K cleanroom, meets the highest standards for medical-grade production. We are ISO 9001 and ISO 13485 certified, ensuring quality management and compliance with the strictest regulations, especially in the medical sector.
With advanced equipment, including over 60 LSR machines, we provide fast, reliable, and cost-effective solutions tailored to our clients’ unique needs.
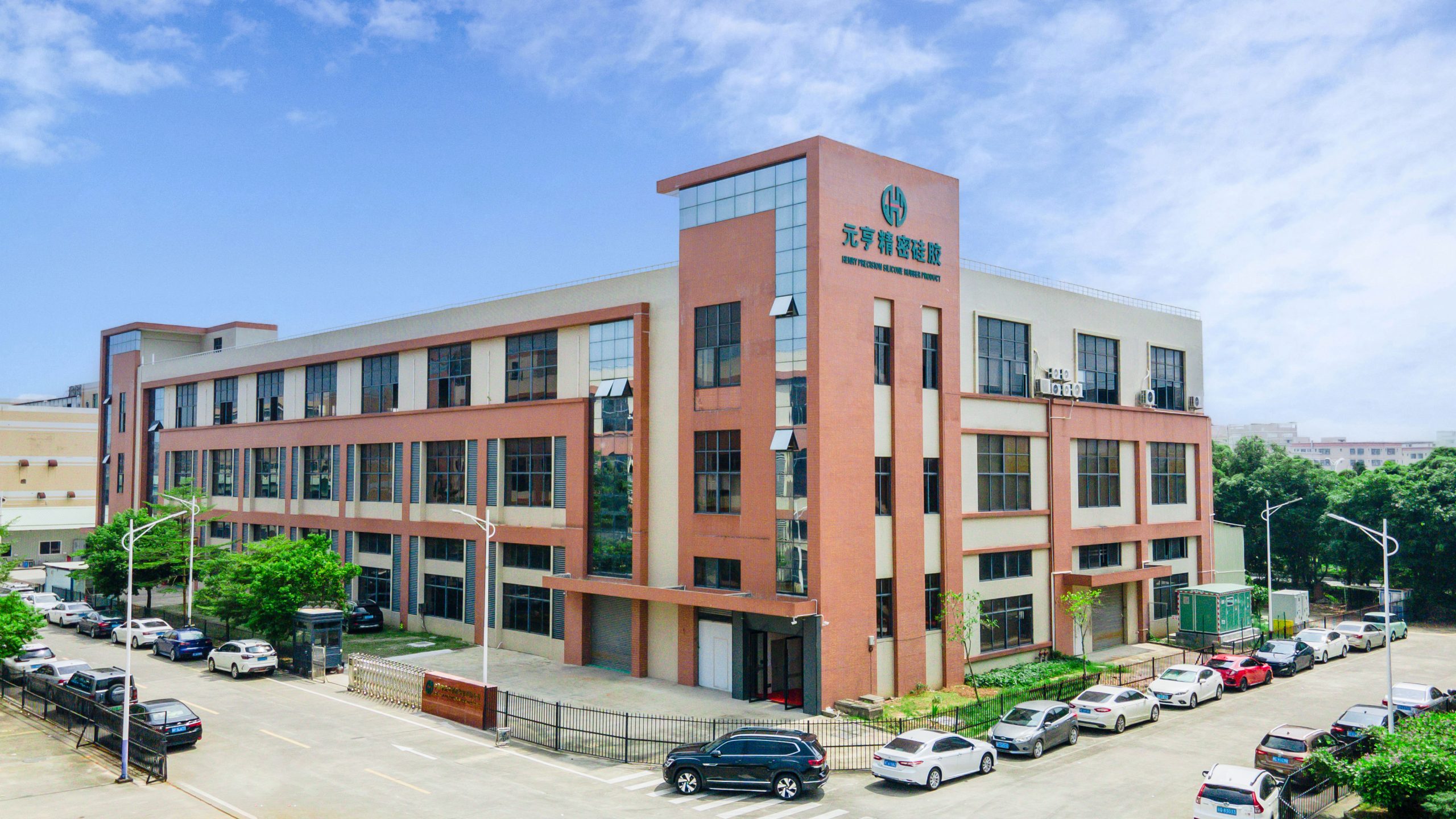
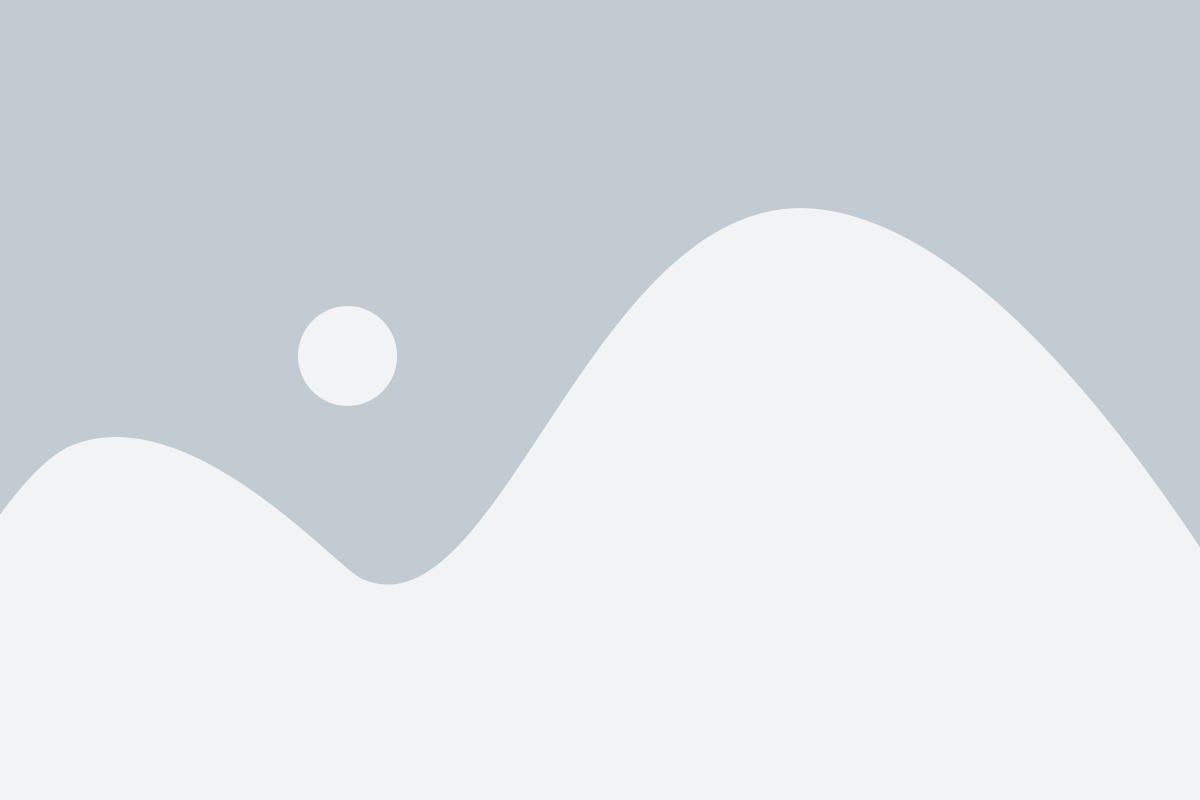
Design & Prototyping Support
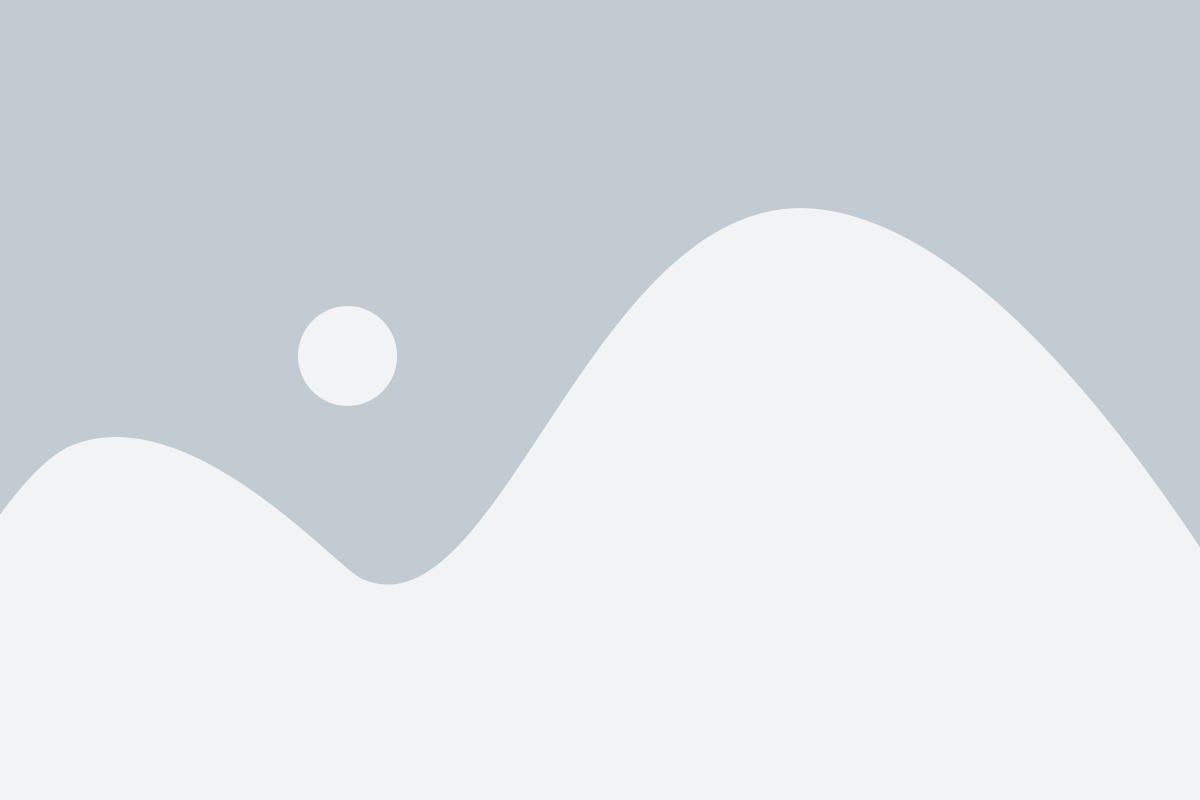
Liquid InjectionMolding
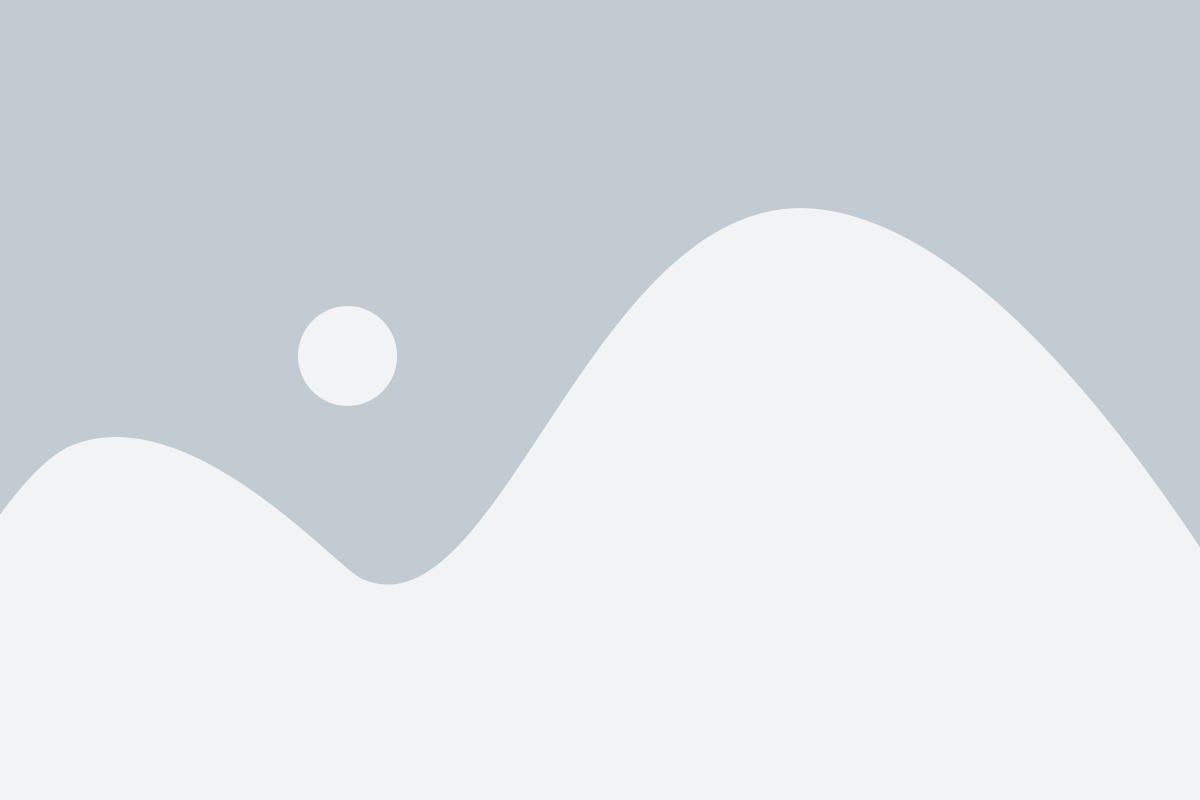
Value-Added Processes
Why Choose Us
Advanced Engineering Expertise
Our team of 15 skilled engineers, including a Siemens Bronze Mold Flow Analyst and a National Certified Senior Mold Engineer, ensures that we deliver cutting-edge, high-precision solutions. We also have a specialized department for silicone precision molds.
Comprehensive Quality Assurance
We are ISO 9001, ISO 13485, ISO 45001, and ISO 14001 certified, guaranteeing our commitment to quality management, safety, and environmental responsibility. Additionally, we hold Medical Production License and National High-tech Enterprise Certification, ensuring regulatory compliance and industry-leading standards.
Food & Medical-Grade Cleanrooms
With a 15,000 m² facility, including a 5,000 m² Class 100K cleanroom, we maintain a controlled environment that meets the highest standards for both food-grade and medical-grade production. Our 60+ LSR machines and 10K cleanroom for plastics enable us to produce high-quality products efficiently.
Exceptional Testing Capabilities
Our 200 m² specialized laboratory offers extensive silicone performance testing, with the flexibility to create custom testing solutions tailored to meet our clients' unique requirements.
Cooperation Process

Request a Quotation
Upload your 2D/3D files and product details. Our team will review the submission and provide an accurate quotation within 24 hours, ensuring a quick and efficient start to your project.

Confirm the order
Upon confirming the purchase order, we deliver a detailed Manufacturing Analysis Report. This report reviews tolerances, cosmetic specifications, and identifies any potential quality-impacting issues for your approval.

DFM Review
Collaborating with you, we refine mold flow analysis, dimensions, tolerances, and appearance specs. Your timely approval of Design for Manufacturing (DFM) Review ensures optimized production planning.

Production & Quality Assurance
With DFM approval, our dedicated project engineers oversee the entire production process. Inspections are performed under ISO9001 and ISO13485 standards to ensure precision and consistency.

Timely Delivery & After-Sales Support
After quality assurance checks, parts are packaged and delivered promptly. Our team remains available to address any post-delivery concerns, ensuring your complete satisfaction.
Global Partners
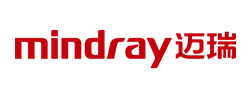
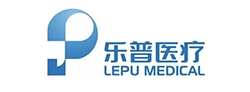
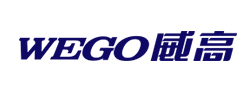
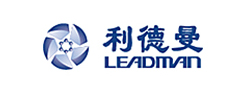
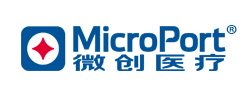
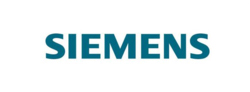
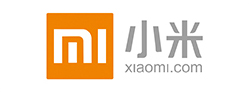
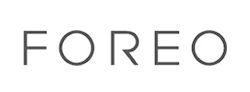
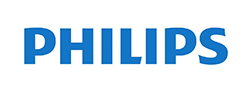
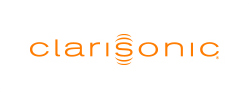
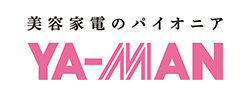
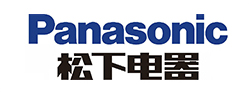
Plant display
Cases
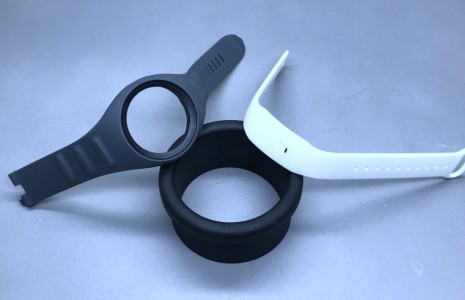
This is an editable piece of text,This is an editable piece of text,This is an editable piece of text,
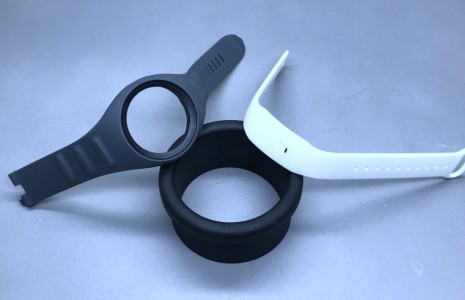
This is an editable piece of text,This is an editable piece of text,This is an editable piece of text,
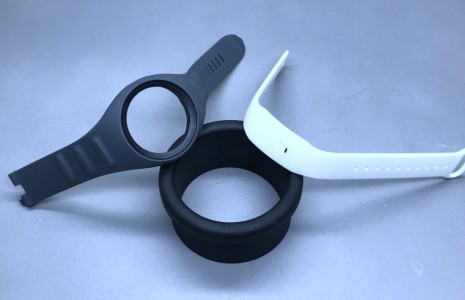
This is an editable piece of text,This is an editable piece of text,This is an editable piece of text,
Let’s build the future with innovation.
Please provide the following details to help us better understand your needs and get in touch with you as soon as possible.
You can send us 3D drawings in STL, STEP, IGES and 2D drawings in PDF. We will provide accurate quotations within 24 hours.
From concept to completion, we provide a one-stop silicone mold manufacturing service.