For this project, Henry Precision was tasked with producing a respiratory mask using a rapid prototype mold. The product was made from Liquid Silicone Rubber (LSR) and required precise manufacturing to meet high standards. The mold size was Wx300 Lx300 H (mm), and it featured a cavity of 1. The delivery time was set at 10 days to meet the customer’s needs.
Manufacturing process | Rapid prototype mold (referred to as sample mold) |
Material | LSR |
Insert Material | Steel S136 |
Product size | 124x109x73mm |
Mold size | Wx300 Lx300 H (mm) (Lung Kee standard mold holder: 3030) |
Cavity | 1 |
Delivery time | 10 days |
Manufacturing Process
The rapid prototype mold, also known as the sample mold, was used for this project. This method is cost-effective and efficient, offering high-speed machining and reliable design solutions. It is ideal for producing parts quickly while maintaining accuracy and quality.
The mold was produced using Henry’s standard mold holder. This system ensures modularity and reusability, which reduces both lead time and mold costs. Unlike conventional molds, which require die holders from suppliers with long lead times, Henry’s rapid prototype molds offer a faster and more economical alternative.
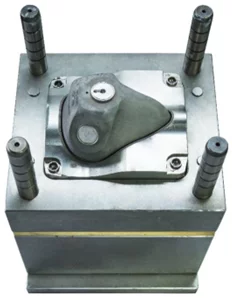
Material and Tooling Details
The product was manufactured using LSR, which is ideal for medical-grade products due to its durability and flexibility. The insert material was Steel S136, a material known for its high resistance to wear and corrosion.
Henry’s prototype tooling life spans from 500 to 50,000 die runs, depending on the steel type used. For this project, P20 or NAK80 steel was chosen to meet the customer’s needs. The tooling was designed for reusability, reducing the overall cost of the project.
Project Features
- Lead Time: The lead time for prototype molds is typically 1-2 weeks, with more complex or larger molds requiring up to 4 weeks. For this project, the mold was delivered within 10 days, meeting the customer’s tight timeline.
- Cost Efficiency: Henry’s standard mold holder helped reduce costs by eliminating the need for custom die holders. This feature, along with modular components, allowed for significant cost savings.
- Quality and Precision: The mold was produced with high precision. Henry’s team provided a DFM (Design for Manufacturability) report before production. This report included parting lines, gate locations, ejector positions, and other critical specifications. The customer confirmed these details, ensuring the product would meet all quality standards.
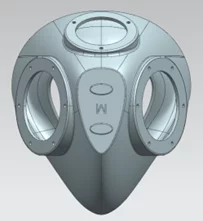
Prototype Tooling and Adaptability
During product development, engineering changes are often needed. Henry’s prototype tooling is adaptable, allowing for adjustments after sampling. However, if customers request changes, additional charges may apply. The tooling was designed to last, and after two years of storage, it can be scrapped or repaired as per the customer’s request.
Results
By using rapid prototype molds, Henry was able to deliver the respiratory mask within a short lead time while maintaining high quality. The use of standard mold components minimized costs and production time, offering the customer a highly efficient solution.
The project showcases how Henry’s rapid prototype mold process, with its standardized tooling and modular approach, provides a reliable and cost-effective solution for the production of medical-grade products.
If you have any new project, please contact us now for a free quote!