Project Overview: High-Temp Resistance & Precision Sealing
In the e-cigarette industry, silicone components (such as sealing rings, mouthpieces, and anti-leak gaskets) must meet food-grade safety, high-temperature resistance, and ultra-low leakage rates. To meet the high standards of a well-known e-cigarette brand, Henry Precision developed high-temperature-resistant, ultra-precise, and mass-producible silicone sealing components, completing the full process from design to mass production in just 116 days.
📅 Project Duration: Nov 15, 2024 – Mar 10, 2025 (116 days)
🎯 Key Challenges: 250°C heat resistance, ≤0.01mm leakage rate, ±0.01mm tolerance
🔧 Technical Innovations: 8-cavity mold, matte surface treatment, plasma surface modification
🚀 Final Results: Daily capacity 25,000 pcs, 98.8% yield rate, 22% cost reduction
1. Design Phase: Precision & High-Temp Durability
📌 Design Objectives:
✅ Food-Grade Silicone – Compliant with FDA 21 CFR 177.2600 and RoHS 2.0
✅ High-Temperature Resistance – Long-term stability at 250°C, no deformation or aging
✅ Sealing Performance – ≤ 0.01mm leakage rate, ensuring zero e-liquid leakage
✅ Surface Treatment – Matte coating (Ra 0.8-1.6μm) for an anti-glare, premium feel
✅ Durability Test – 100,000 open-close cycles with no fatigue deformation
📌 Technical Challenges:
🔹 ±0.02mm micro-sized sealing ring tolerance for consistent performance
🔹 Silicone + PC overmolding bonding strength optimization to prevent delamination
🔹 Compression set resistance ≤15% under high temperatures for long-lasting sealing
🔹 Ensuring uniform matte surface finish across mass production batches
📅 Key Milestones:
📌 Nov 15-25 – Competitor teardown & failure analysis
📌 Nov 26-Dec 5 – 3D modeling (UG NX)
📌 Dec 6-10 – Finite element simulation verification (COMSOL)
2. Mold Design: Multi-Cavity Molding for Efficiency
📌 Innovative Solutions:
✅ 8-Cavity Mold: Boosts production efficiency by 300%
✅ Needle Valve Hot Runner: Eliminates weld lines for a cleaner finish
✅ Gas-Assisted Demolding: Facilitates complex sealing ring release
✅ Modular Core Inserts: Allows quick mold changes in under 5 minutes
📌 Key Machining Challenges:
🔹 Ra 0.4μm mold cavity surface for optimal silicone flow and smooth finish
🔹 ±0.01mm tolerance for sealing rings to ensure long-term sealing performance
🔹 Multi-insert concentricity ≤0.02mm to prevent misalignment
📅 Key Milestones:
📌 Dec 11-15 – Mold flow analysis (Moldflow Insight)
📌 Dec 16-25 – Electrode design & structure testing
📌 Dec 26-Jan 5 – CNC machining (H13 tool steel, DMG machine)
3. Trial Production & Optimization
📌 Trial Production Parameters:
🟢 Material: Shin-Etsu HTV-4210 (Shore A50)
🟢 Curing Conditions: 180°C × 90s
🟢 Capacity: 800 pcs per mold per 8-hour shift
📌 Issues & Optimization Strategies:
❌ Oversized sealing rings (Feb 3-5) ➡️ Closed-loop mold temperature control (180°C ± 0.5°C)
❌ Inconsistent surface gloss (Feb 7-10) ➡️ Optimized matte coating spray parameters
❌ Poor adhesion between silicone and PC (Feb 12-15) ➡️ Plasma surface treatment (dyne value ≥50 dyn/cm)
📅 Key Milestones:
📌 Jan 20 – Passed FDA food contact certification
📌 Jan 25 – Completed 250°C high-temp aging test (1000 hours)
📌 Feb 1 – Passed IP67 waterproof test (1m depth, 30 min)
4. Mass Production & Efficiency Boost
📌 Mass Production Optimization:
✅ Reduced curing time to 75s (optimized catalyst concentration)
✅ Mold change time reduced to 15 min (hydraulic quick-positioning system)
✅ AI Vision Inspection System – 0.01mm precision, ensuring 100% quality control
📌 Final Production Achievements:
🚀 Daily capacity: 25,000 pcs (3 shifts)
🚀 Yield rate: 98.8% (up from 93.5% in trials)
🚀 Cost reduction: 22% (longer mold lifespan)
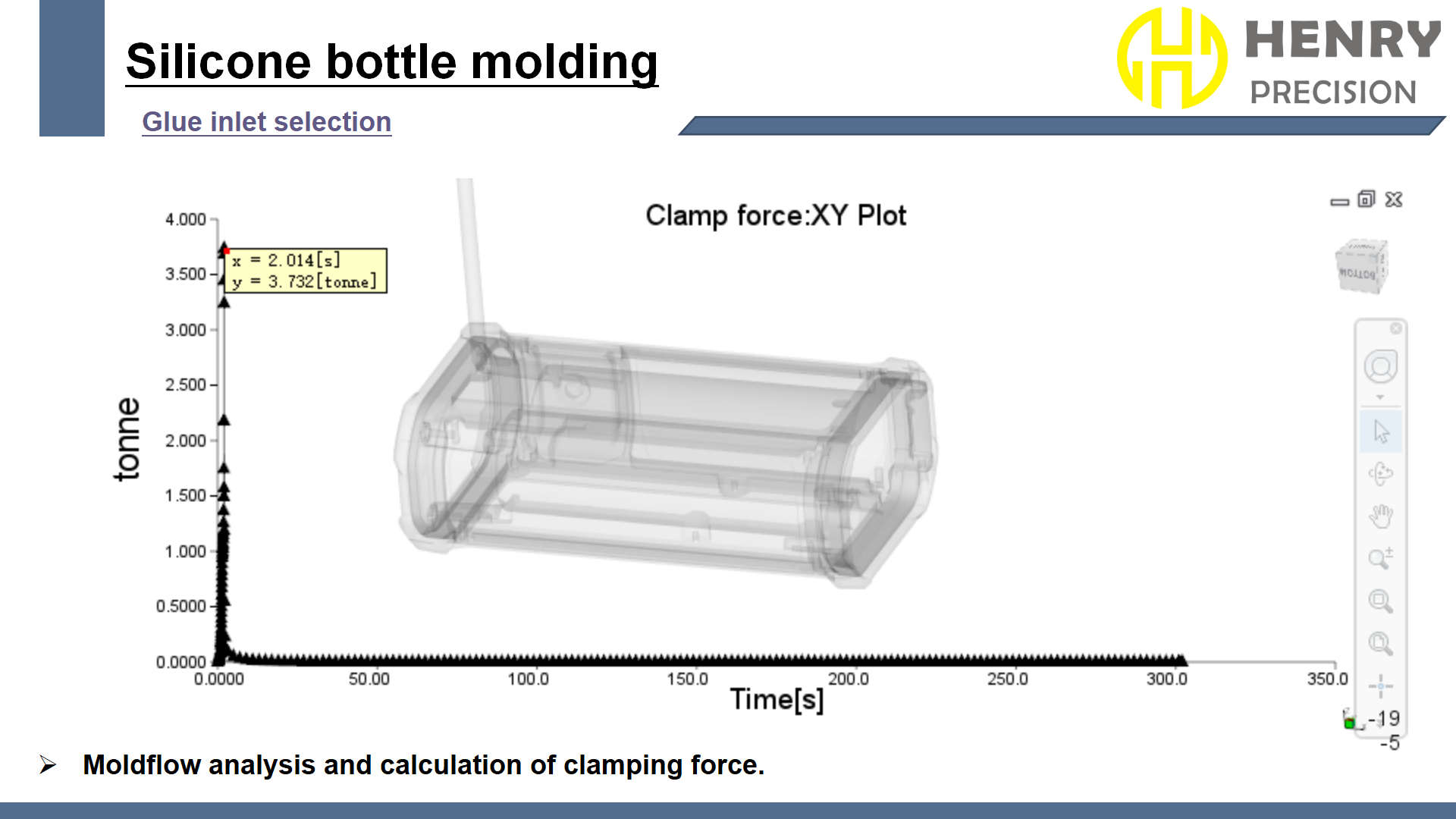
Case Summary: Why Choose Henry Precision?
✅ High-Temperature Sealing: Optimized curing ensures stable performance at 250°C
✅ Micro-Sized Precision: Multi-directional core pulling molds achieve ±0.01mm tolerance
✅ Consistent Matte Finish: Specialized coating technology ensures uniform Ra 0.8-1.6μm
✅ High Production Efficiency: 8-cavity mold + AI inspection, boosting capacity by 300%
Need high-precision, heat-resistant silicone parts?
📩 Contact us for a custom solution!
🔗 LSR Injection Molding
🔗 Custom Silicone Parts
📞 Phone: +86 18576001817
📧 Email: gina@henry-precision.com
💡 Contact us today to start your project! 🚀