In the production of sealing rings for medical devices, maintaining precision and ensuring high-quality performance is crucial. Henry Precision recently encountered several challenges while manufacturing a sealing ring with WACKER 3038-70 silicone material. The product’s small size, internal instability, and complex structure required advanced design, meticulous attention to detail, and high-precision mold processing.
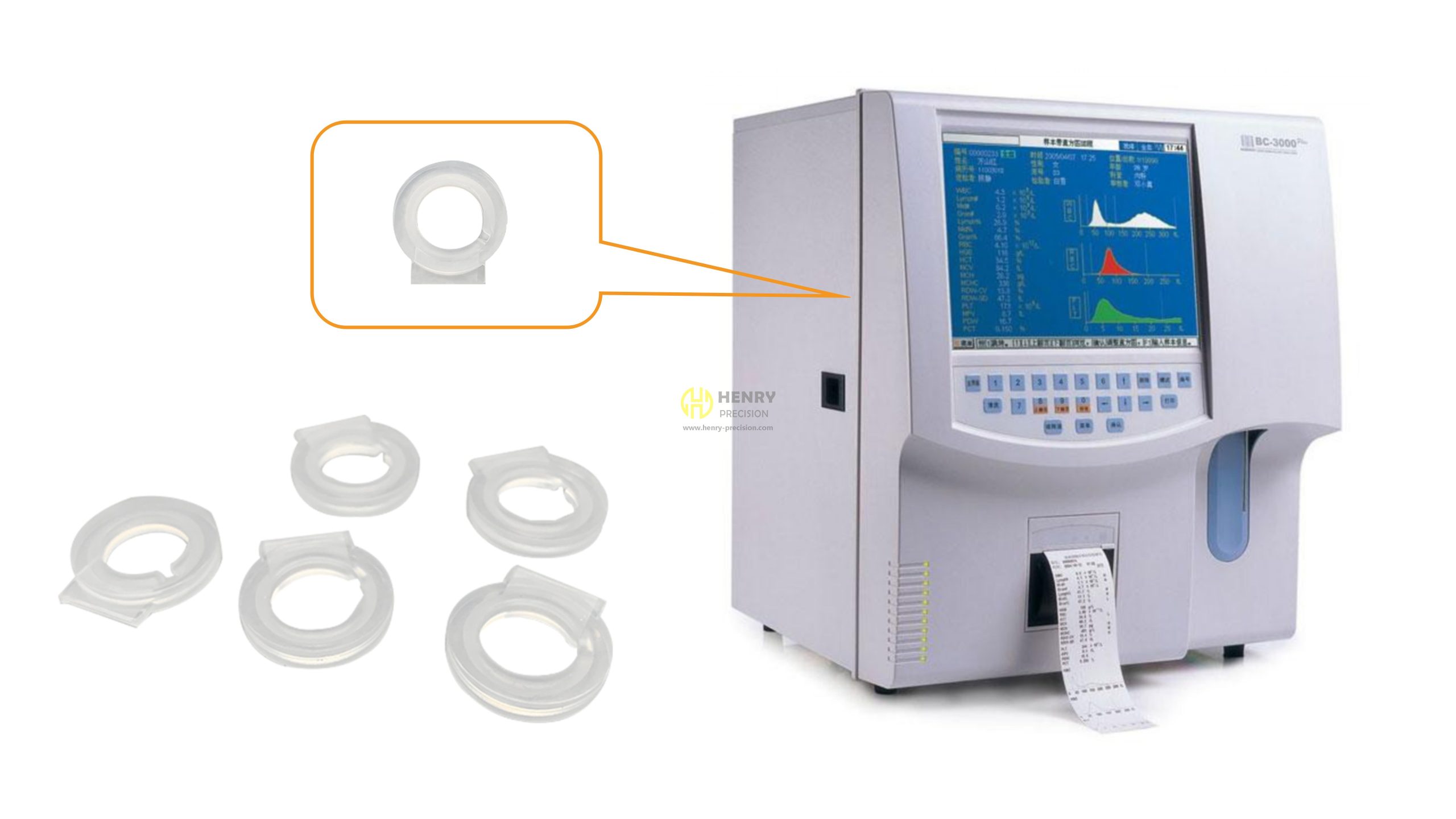
Challenges
- Internal Size Instability
The sealing ring had a relatively small internal size, which was prone to instability. This caused issues such as partial silicon filling, leading to potential quality defects. The solution required careful mold design and machining precision to ensure stable production. - Multiple Cavities and Gas Trapping
The product featured a high number of cavities, making it susceptible to trapped gas, bubbles, and appearance defects. This required an optimized raw material distribution, temperature control in the mold, and higher equipment stability. The need for precise control over the injection process became apparent to prevent these defects. - Appearance Defects Due to Flash Burrs
The inner ring of the sealing ring had a tendency to develop flash burrs, affecting the appearance of the product. This demanded high levels of mold precision and stable molding equipment to avoid such defects and ensure product integrity. - Large Production Demand
The customer had a large demand for sealing rings, necessitating the development of high-quality tooling. With a tool design involving 1×64 cavities, the company needed to make significant technical breakthroughs to meet the production scale. Achieving this required innovation in mold design and precision engineering, positioning Henry Precision as an industry leader in mass production. - Thin Mold Design
The sealing ring required the use of a thin steel mold, with the thinnest area measuring just 0.2mm. This thin design posed challenges to the mold’s structural integrity, making mold design and processing even more critical. The required precision in mold processing equipment was heightened to ensure consistent quality.
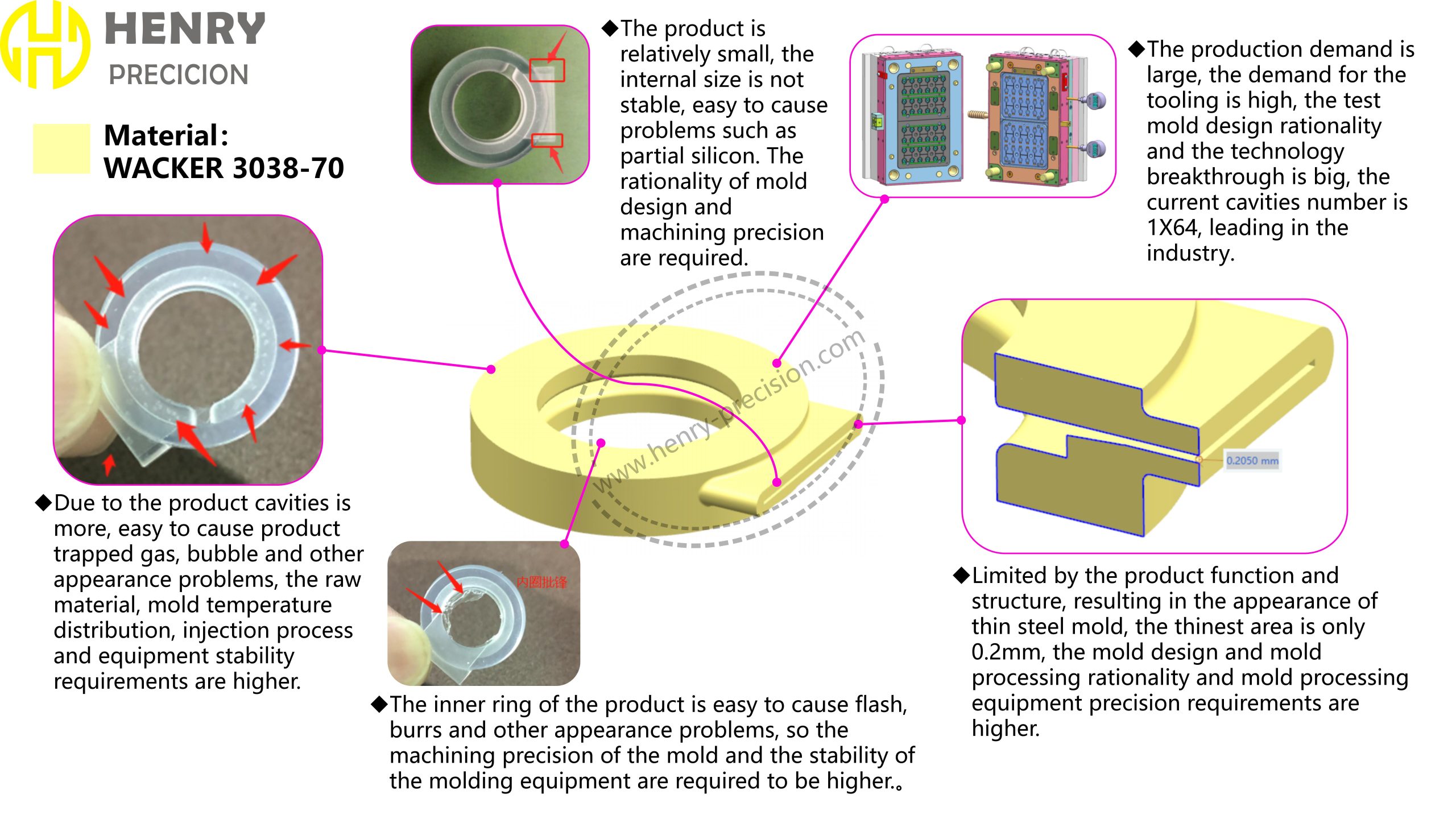
Results
By leveraging WACKER 3038-70 silicone material, optimized mold design, and advanced molding technology, Henry Precision successfully produced high-quality sealing rings for medical devices. The solution met all the functional and aesthetic requirements, passing stringent medical device standards. The sealing rings exhibited excellent performance in real-world applications, with no defects or quality issues, and the production process was both cost-effective and efficient.
This case study highlights the challenges of producing medical sealing rings and the innovative solutions Henry Precision implemented. By focusing on material selection, mold design, and production process optimization, Henry Precision delivered a product that met the highest standards of quality and performance. This case demonstrates Henry’s commitment to excellence in medical device manufacturing and its ability to tackle complex production challenges.