With the increasing prevalence of intelligent medical devices and minimally invasive surgeries, the application of surgical robots has become more widespread. The gas and liquid transmission system of surgical robots is one of its core components, used to precisely control the flow of gases and liquids during surgical procedures. However, existing connector products fall short in terms of biocompatibility, reliability, and miniaturized design, failing to meet the demands of high-end medical equipment. Therefore, a multinational medical device manufacturer commissioned us to develop a new type of silicone connector for its latest generation of surgical robots.
The connector is required to meet the following three core requirements:
- Biocompatibility: Pass the ISO 10993-5 cytotoxicity test and USP Class VI certification to ensure the product is safe and non-toxic in contact with the human body.
- High Reliability: Withstand 100,000 cycles of dynamic plug-in and pull-out life to meet the long-term, high-intensity usage demands of surgical robots.
- Miniaturized Design: Integrate an EMI shielding layer into a dual-channel structure while ensuring dimensional accuracy and functionality to fit the compact internal space of surgical robots.
The project timeline spans from November 15, 2024, to March 10, 2025, totaling 116 days.
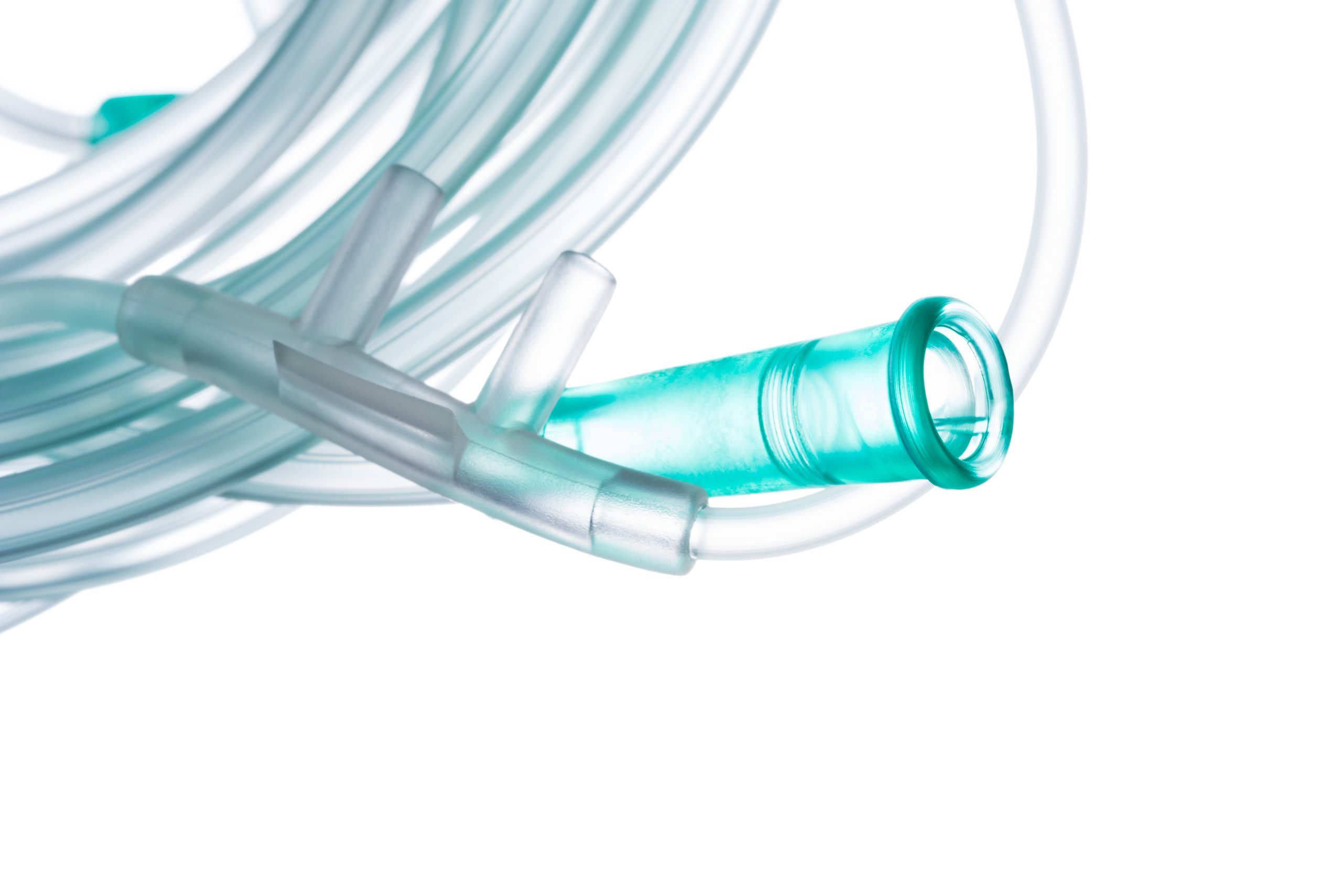
Design Phase: Breaking Through the Technical Bottlenecks of Miniaturized Structures
3D Modeling and Simulation Analysis
- High-Precision Modeling:
- Utilized CATIA V5 software to build a 3D model with a positioning accuracy of ±0.1mm to ensure the precision of the anti-misinsertion structure. The design team closely communicated with the client, optimizing the connector’s interface shape and dimensions based on the actual needs of the surgical robot.
- Employed parametric design to quickly adjust model parameters to meet the client’s requirements for different specifications of the connector.
- Dynamic Sealing Pressure Distribution Simulation:
- Conducted finite element analysis using ANSYS software to simulate the dynamic sealing pressure distribution of the connector during use. Through simulation, the lip thickness gradient was optimized from 0.8mm to 1.2mm to ensure the reliability of sealing performance under high pressure and dynamic conditions.
- Introduced finite element analysis (FEA) to assess the strength of the latch structure. By simulating 100,000 cycles of plug-in and pull-out processes, the strength and durability of the latch under high stress were verified to ensure no plastic deformation.
Multi-Material Injection Molding Design
- Material Selection:
- The inner layer uses German Wacker HTV-4210 silicone (Shore A50), which offers excellent biocompatibility and elasticity, meeting the stringent requirements of medical devices.
- The outer layer is covered with PBT engineering plastic to integrate the EMI shielding layer, ensuring the connector’s stability in electromagnetic environments.
- Innovative Interface Structure:
- Designed a “mushroom head” interface structure, which enhances the bonding strength between materials to 15MPa through special geometric shapes and surface treatments, effectively preventing delamination and peeling.
- Employed multi-material injection molding technology, optimizing injection parameters to ensure perfect bonding between silicone and PBT plastic.
Failure Mode and Effects Analysis (FMEA)
- Risk Identification:
- Identified critical risk points, such as the difficulty in demolding the micro latch (Risk Priority Number, RPN = 96). Due to the small size and complex structure of the latch, it is prone to damage or deformation during the demolding process.
- Preventive Measures:
- Designed a multi-directional core-pulling mechanism to achieve smooth demolding of the complex latch through precise mold design and mechanical structure.
- Introduced a gas-assisted demolding system, using high-pressure gas to assist in demolding, reducing demolding force and minimizing the risk of latch damage.
Mold Development: A Technological Revolution in Precision Manufacturing
Mold Scheme Innovation
- Modular Combination Mold:
- Adopted a modular design to enable rapid switching of four types of core pins, meeting the production needs of different specifications of connectors. The modular design not only enhances the mold’s versatility and flexibility but also reduces mold change time.
- Hot Runner System Optimization:
- Configured a hot runner system with needle valve gates, precisely controlling the flow of molten material to achieve a flow balance rate of 98.7%. The optimized hot runner system reduces shear heat and pressure loss in the molten material, improving product quality.
- Independent Temperature-Controlled Water Circuit System:
- Designed an independent temperature-controlled water circuit system to strictly control the cavity temperature difference within ±1.5℃. Through precise temperature control, the dimensional accuracy and surface quality of the connector are ensured.
Precision Machining Technology
- High-Precision Machining Equipment:
- Utilized a DMG MORI five-axis machine tool to process H13 tool steel, ensuring high-precision machining of mold cores and cavities. The high-precision machining capability of the five-axis machine tool provides strong support for the manufacture of complex mold structures.
- Surface Treatment and Precision Control:
- The mold core surface was polished to a mirror finish, achieving a surface roughness of Ra0.2μm, with a tolerance control of ±0.01mm. Mirror polishing not only improves the mold’s surface quality but also reduces friction and wear during the injection molding process.
- For complex cavities, graphite electrodes were used for electrical discharge machining (EDM), with a discharge gap controlled within ±5μm, ensuring high-precision cavity formation.
Mold Verification System
- Precision Inspection:
- Used a coordinate measuring machine to inspect the key dimensions of the mold, conducting inspections twice a week to ensure the mold’s precision meets design requirements.
- Life Pre-Experiment:
- Conducted a 500,000-cycle open-and-close life pre-experiment, with an initial 3,000-cycle trial molding to verify the mold’s durability and stability.
- Pressure Test:
- Performed a pressure test on the mold at 180kg/cm² to verify the flash control capability, ensuring no burrs or overflow during the injection molding process.
Pilot Production Optimization: Precise Adjustment of Process Parameters
Initial Process Parameters
- Vulcanization Process:
- The vulcanization temperature was set at 175℃ with a vulcanization time of 120 seconds to ensure complete curing and good mechanical properties of the silicone.
- Injection Molding Process:
- The injection pressure was 120MPa with a holding time of 25 seconds to ensure the material fully filled the cavity and minimized internal defects.
- Production Capacity Assessment:
- The initial production capacity was 400pcs per 8 hours, meeting the demand for small-batch pilot production.
Key Issues and Solutions
- Latch Shrinkage Issue:
- Increased the holding time to 35 seconds and optimized the gate position to ensure the material fully flowed and cured within the cavity, reducing shrinkage.
- EMI Shielding Layer Peeling Issue:
- Adjusted the injection molding temperature gradient, raising the injection temperature of PBT plastic from 185℃ to 195℃ to improve the bonding strength and interfacial strength.
- Dimensional Fluctuation Issue:
- Implemented closed-loop temperature control of the mold, maintaining the mold temperature at 180℃ ±0.5℃ to reduce dimensional variations caused by temperature fluctuations.
Quality Improvement Data
- Sealing Performance Optimization:
- The leakage rate was reduced from 0.3ml/min to 0.05ml/min, significantly improving sealing performance to meet the stringent requirements of the gas and liquid transmission system in surgical robots.
- Enhanced Consistency of Plug-in and Pull-out Force:
- The CPK value of plug-in and pull-out force increased from 1.2 to 1.67, ensuring the reliability and consistency of the connector during dynamic plug-in and pull-out processes.
- Biocompatibility Verification:
- Passed the USP Class VI extractable test, ensuring the product meets international standards for biological safety.
Mass Production Phase: Dual Breakthroughs in Efficiency and Cost
Process Innovation
- Optimization of Vulcanization Time:
- By adding 0.3% platinum catalyst, the vulcanization time was reduced to 90 seconds, significantly improving production efficiency.
- Reduction of Mold Change Time:
- The adoption of a hydraulic quick positioning system reduced mold change time from 45 minutes to 25 minutes, further enhancing equipment utilization.
- Introduction of Automated Inspection Technology:
- A machine vision inspection system was introduced to achieve 100% dimensional inspection of all products, ensuring that each item meets quality standards.
(2) Production Capacity Improvement Data
- Daily Output per Mold:
- Increased from 400pcs per 8 hours during the pilot production phase to 1,500pcs per day (three-shift system) in mass production, representing a substantial increase in output.
- Yield Rate:
- Improved from 94.7% in the pilot production phase to 98.2% in mass production, significantly enhancing product quality.
- Unit Cost Reduction:
- Through the optimization of processes, the unit cost was reduced by 15%. The mold life was extended from 500,000 cycles to 800,000 cycles, contributing to cost savings.