During the production process of a certain automotive oil seal accessory, we encountered several key problems: the product size after vulcanization was too small, indentations and glue marks appeared on the surface, and the rubber-coated surface was easy to peel off. By analyzing and solving these problems, we optimized the production process and successfully improved product quality and production efficiency.
Operation Process:
- Apply Adhesive A: First, apply adhesive A evenly on the surface of the metal part. To ensure the effect, the coating layer should be kept as thin and uniform as possible, the thinner the better. Then cool the coated metal part for use.
- Apply Adhesive B: Apply adhesive B on the surface of the metal part coated with adhesive A, and the coating should be as thin as possible. After treatment, place the metal part in an oven at 80 degrees for 10 minutes to ensure that the adhesive is completely cured.
- Product Molding: Put the fluorosilicone rubber and the treated metal part into the mold for vulcanization molding. Key operations include:
- Accurately weigh the fluorosilicone rubber (12g round + 3g head).
- Use an air gun to blow away possible impurities in the mold to ensure the quality of the product.
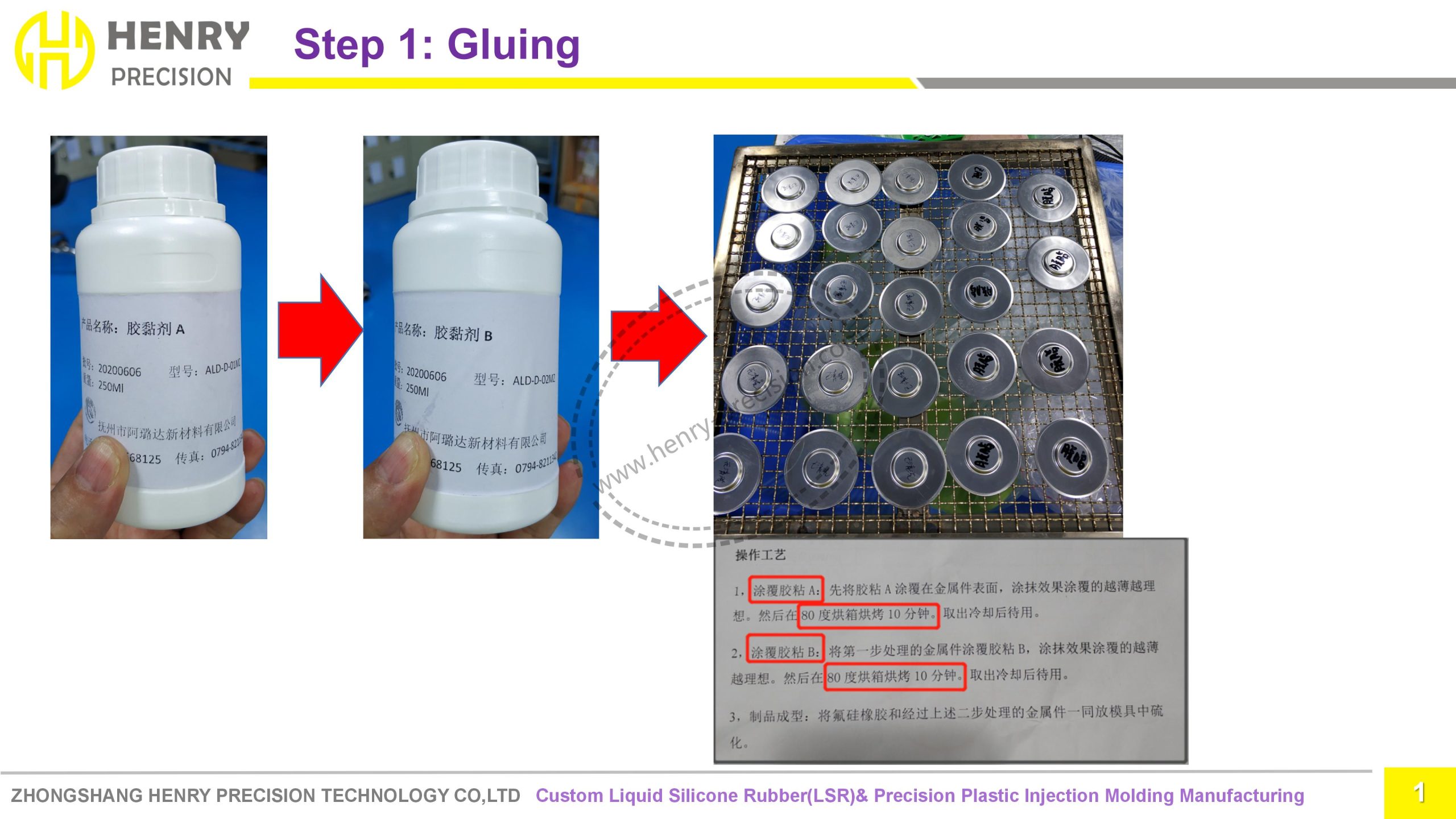
Problem Analysis:
- Small Size: After vulcanization treatment, the outer size of the product is reduced from the theoretical 93mm to 91.81mm, indicating that there is a significant shrinkage problem.
- Surface Defects: There are too coarse indentations and obvious glue marks on the surface of the product, and the wheel marks on the surface of the insert are too conspicuous, affecting the appearance of the finished product.
- Rubber Coating Peeling: After some products are peeled off at any position, the rubber coating surface is easy to peel off, resulting in product quality problems.
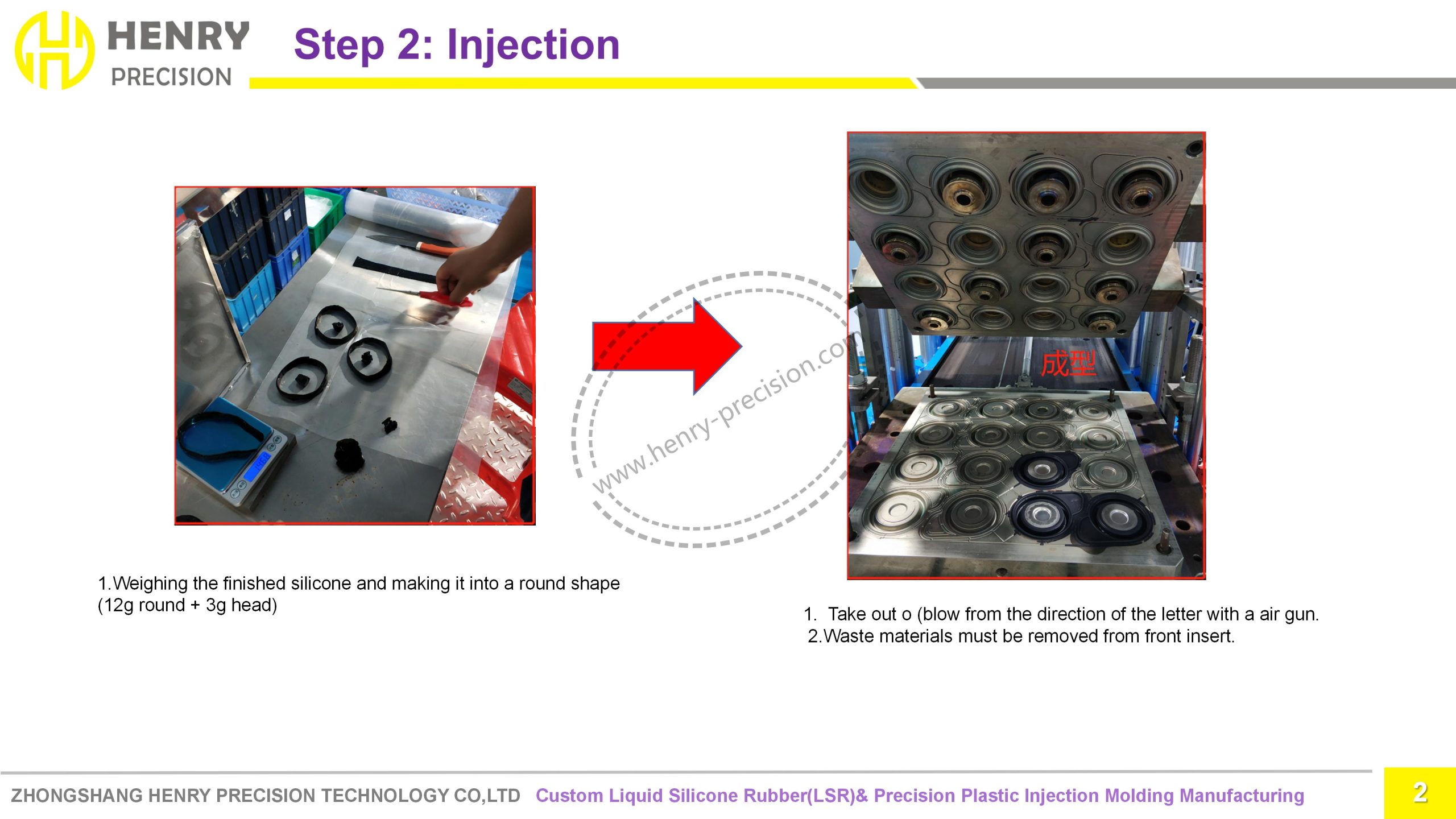
Solutions:
- Small Size Problem:
- Adjust the mold design according to the shrinkage rate of existing products, especially the size of the product periphery.
- Shorten the temperature and time of VOC (volatile organic compound) treatment, reducing the VOC temperature from 200℃ to 180℃, and shortening the treatment time from 4 hours to 2 hours.
- Surface Defects:
- Use a grinder to finely polish the mold surface.
- Test for glue marks using alcohol to ensure no residue.
- Dilute adhesive B with anhydrous ethanol for better bonding.
- Rubber Coating Peeling Problem:
- Improve glue selection for stronger bonding.
- Optimize coating process for more uniform application.
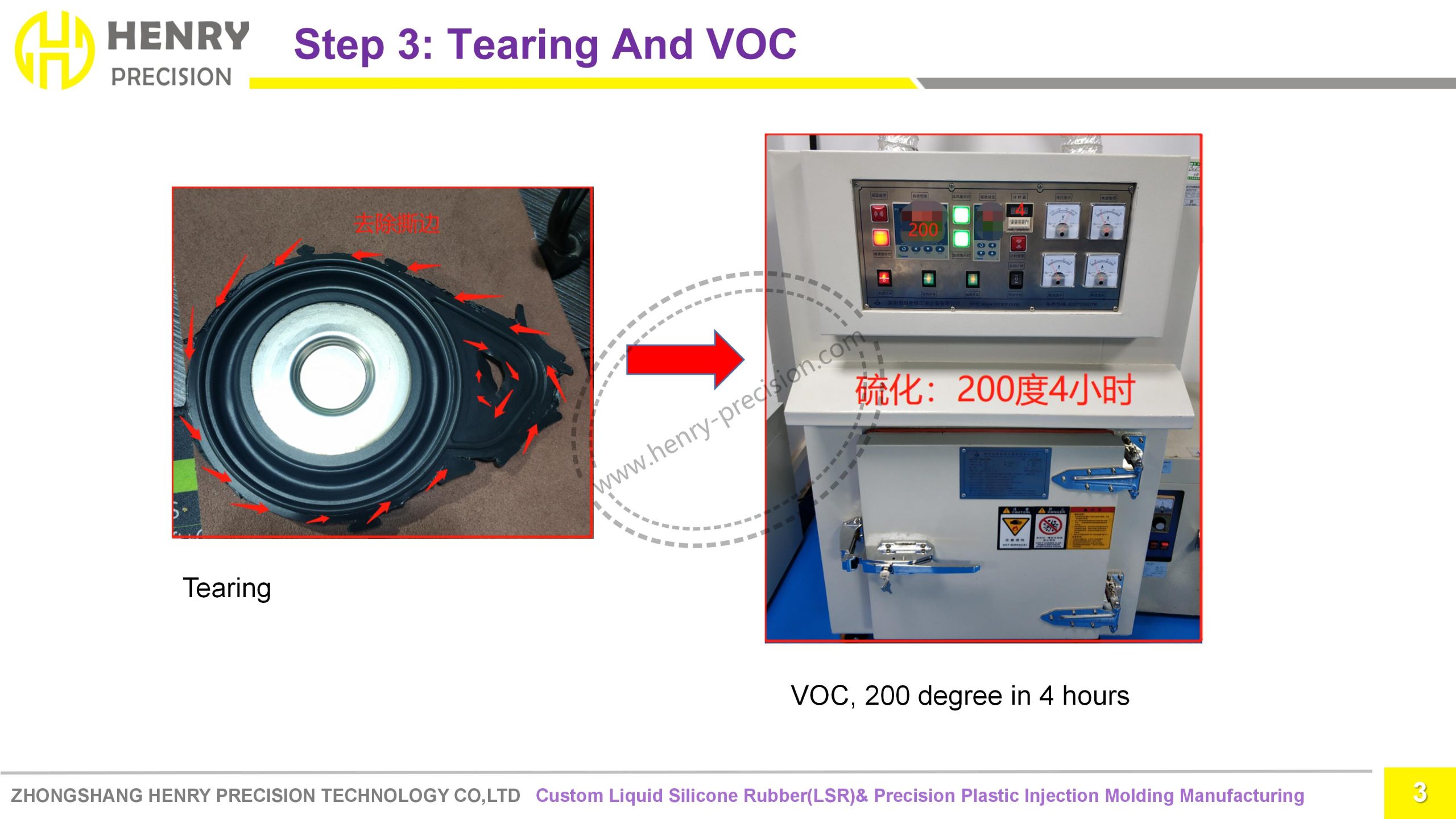
Results:
Through the above optimization measures, the dimensional shrinkage problem in the production process is effectively controlled, surface defects are significantly reduced, and the peeling problem of the rubber surface is also improved. The optimized vulcanization process not only improves production efficiency and reduces scrap rate, but also greatly improves the appearance and functionality of the product.
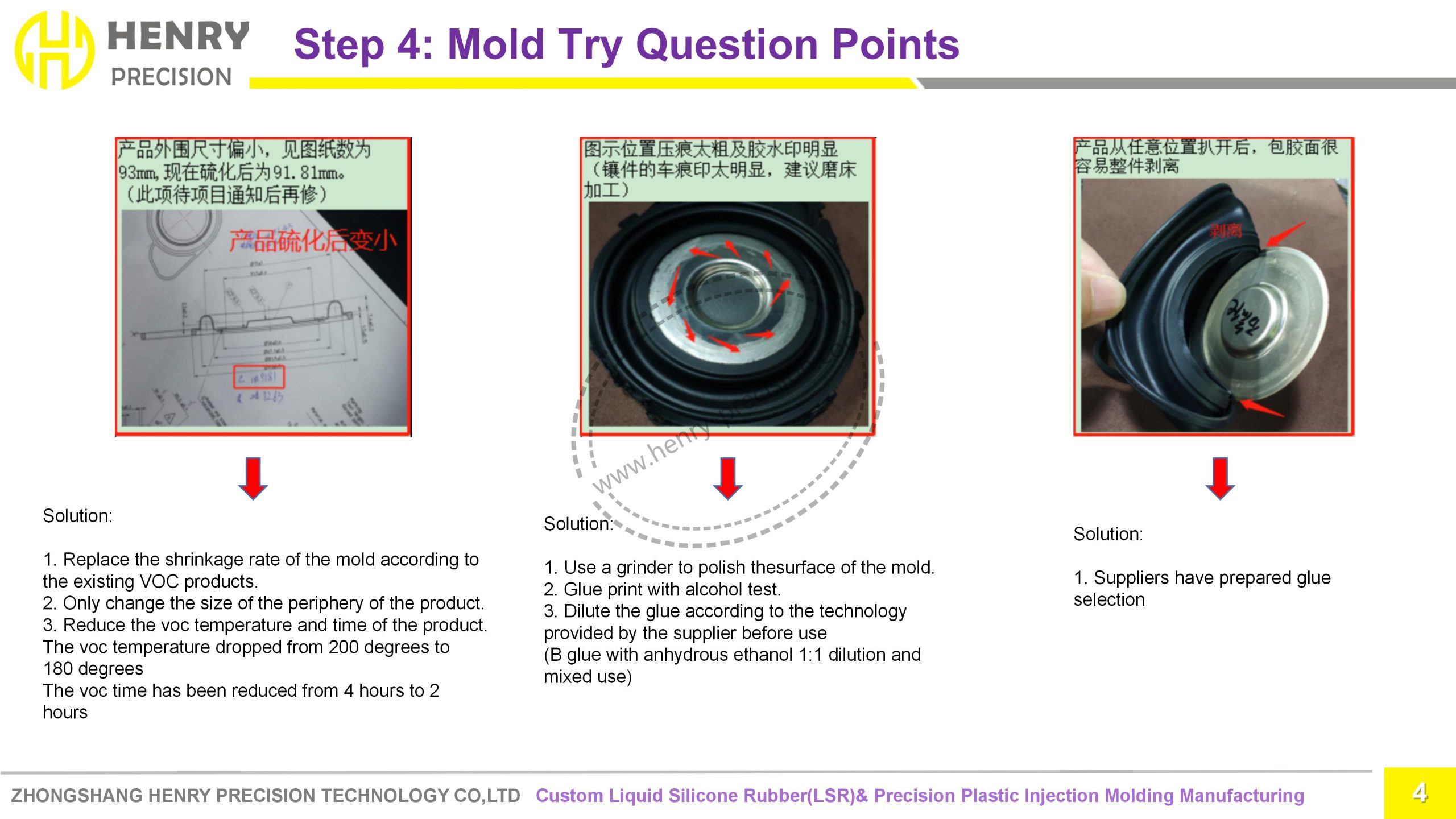
This case demonstrates how optimizing the process of combining fluorosilicone rubber with metal parts successfully addressed common problems like dimensional shrinkage, surface defects, and peeling of the rubber coating. The improvements led to better product quality, higher production efficiency, and enhanced product reliability, offering valuable lessons for similar applications in the automotive seal industry.