Challenges in Medical Mask Production
In medical-grade product production, especially for breathing masks, functionality, safety, and durability are critical. Henry Precision faced several challenges in designing medical masks using Covestro PC-2458 (a high-temperature-resistant polycarbonate) and JAPEN Shin Etsu2090-40 (liquid silicone rubber, LSR). These materials meet FDA’s biocompatibility requirements and provide the necessary support, sealing properties, and performance.
Material Compatibility and Bonding Issues
Bonding liquid silicone to plastic components is essential for maintaining structural integrity. The high fluidity of liquid silicone can cause gas traps, degumming, and non-stick defects. To address this, the adhesive process had to ensure a strong, reliable bond while avoiding contaminants.
Temperature Resistance
Plastic components can only resist temperatures up to 120°C. Exceeding this can cause deformation and twisting, leading to assembly failures. Henry Precision designed a solution to ensure structural integrity even during high-temperature processing.
Appearance Defects
The transparent plastic parts of the masks were prone to visual imperfections such as crashes, deformations, and scratches. Any damage to the surface would affect both the aesthetics and functionality of the product.
Precision in Part Integration
The plastic components had a small outlet diameter of Ф0.8mm with tight tolerances of ±0.05mm. Additionally, the concave structures in the liquid silicone parts created large undercuts that could result in grain defects. Precision molding was essential to prevent cosmetic defects.
Molding Challenges
The liquid silicone had a thin 0.4mm wall thickness, creating long flow paths during molding. This made it prone to air traps and silicone shortages. The molding equipment had to be carefully controlled to ensure stability and high-quality results
Solutions Developed by Henry Precision
To address these challenges, Henry Precision implemented several innovative solutions.
Material and Design Innovation
Our engineers selected Covestro PC-2458 and JAPEN Shin Etsu2090-40, both meeting FDA’s biocompatibility standards. The PC material provided structural support, while the LSR was molded inside the plastic for a secure seal. We achieved tight tolerances to prevent distortion.
Molding Process and Equipment
We used a multi-gate mold flow design, ensuring uniform material distribution. The molds were crafted from S136 mold steel for durability and wear resistance. High-precision Nidoka injection molding machines were used to maintain process stability and prevent defects.
Automated Assembly
We employed robotic technology for assembly. Robots sorted pre-injected thermoplastic parts, placed them on a conveyor, and injected silicone using a liquid injection molding robot. This method ensured reliable bonding and precise integration.
Cleanroom Production
All parts were produced in a 100,000-class dust-free workshop. This environment ensured that the medical-grade components were free from contaminants and met FDA standards.
Results Achieved
By combining high-performance materials, advanced molding techniques, and robotic assembly, Henry Precision overcame the production challenges. The final masks met FDA regulations, with transparent plastic parts maintaining their integrity and aesthetic quality.
Our solution ensured reliable, durable, and high-quality medical masks that met the necessary performance and appearance standards. This case study showcases Henry Precision’s ability to innovate and adapt to complex challenges in the medical device industry.
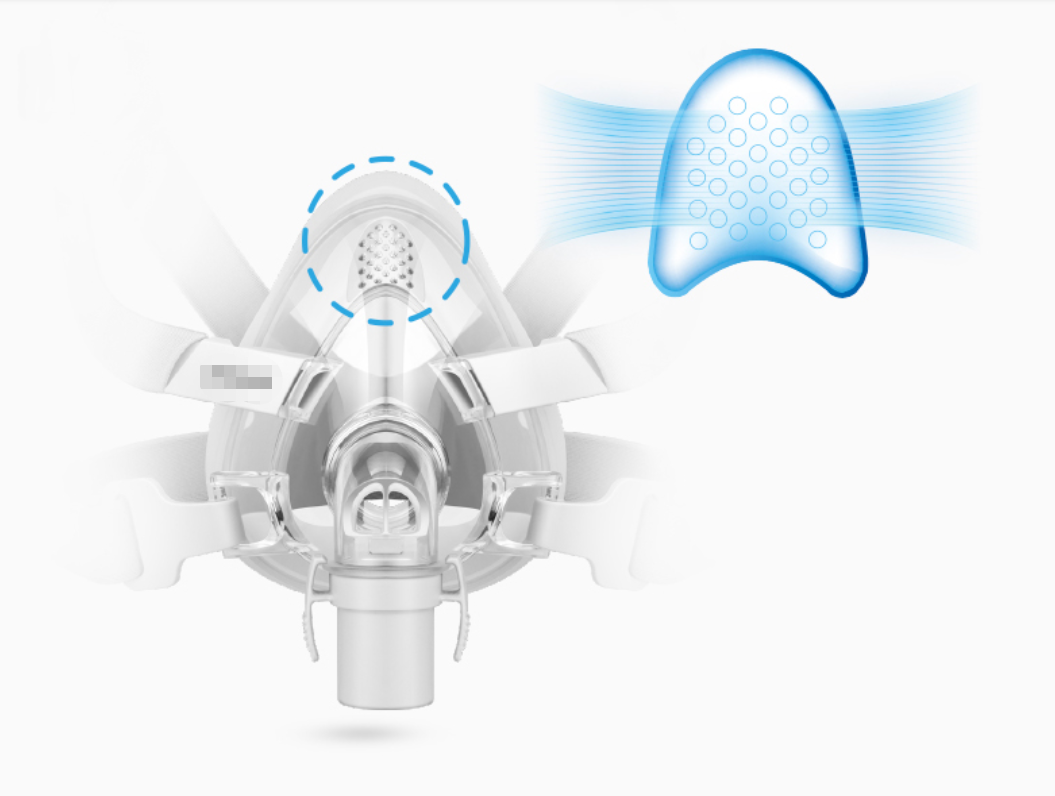