Overview of the Atomizer Aluminum Alloy Shell Project
In this case study, we will explore how we used liquid silicone rubber (LSR) injection molding and precision mold design to produce high-quality atomizer aluminum alloy shells. The project involved several key challenges, including ensuring biocompatibility, durability, and aesthetic quality of the final product. Let’s dive into how we approached the project, from design to production.
Key Challenges in Producing Atomizer Shells
Aluminum Alloy Coating for Corrosion Resistance
The aluminum alloy shells required superior corrosion resistance, especially for skin-contact applications. The solution was to apply a high-performance coating to the aluminum to ensure longevity and maintain product integrity over time.
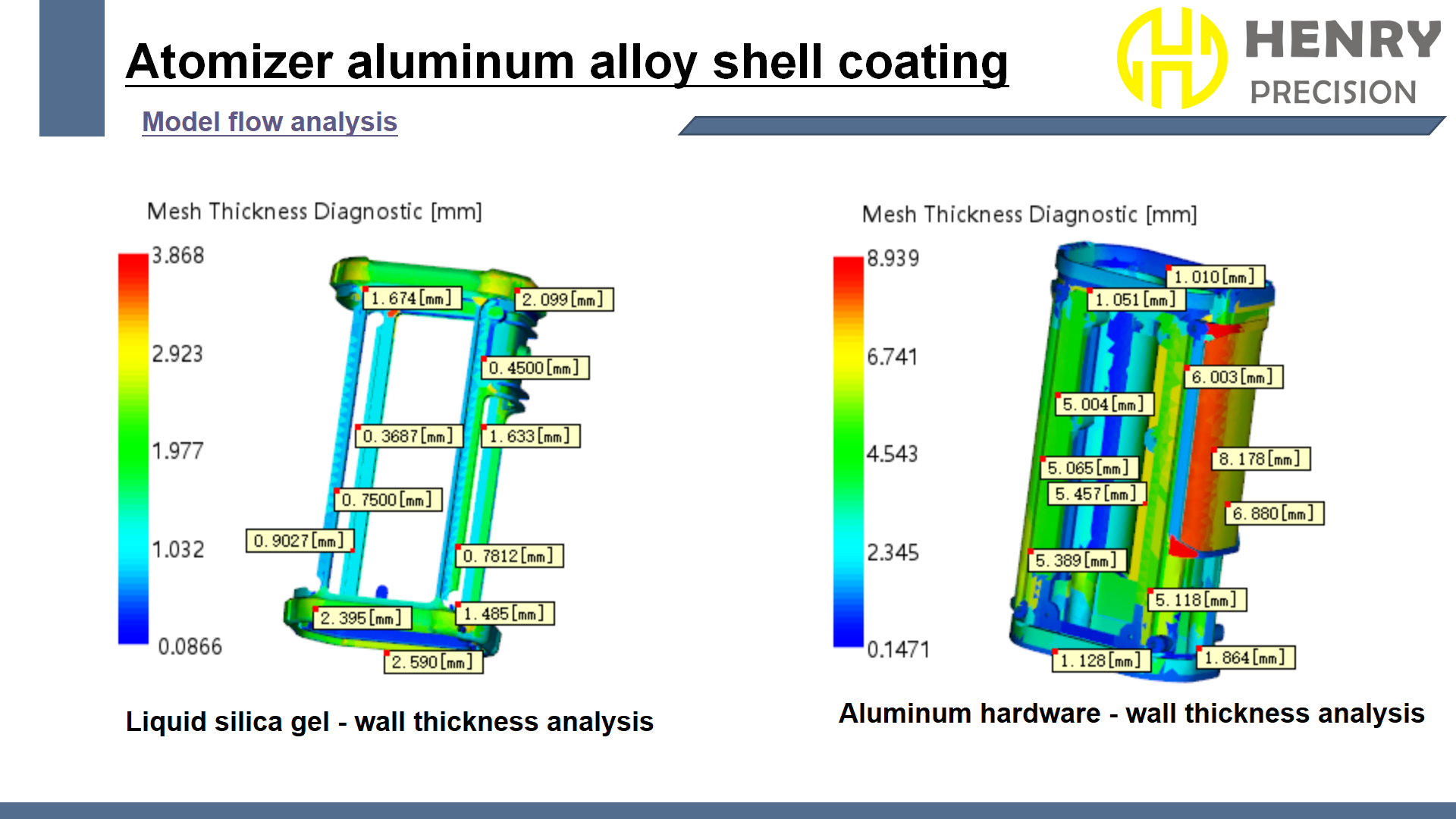
Ensuring Biocompatibility for Skin-Contact Applications
Since the atomizer shell would be in contact with skin, ensuring biocompatibility was a priority. We chose a liquid silicone rubber (LSR) material known for its biocompatible properties, which is also tear-resistant and durable. LSR provides an excellent surface for coating, offering the required flexibility and strength.
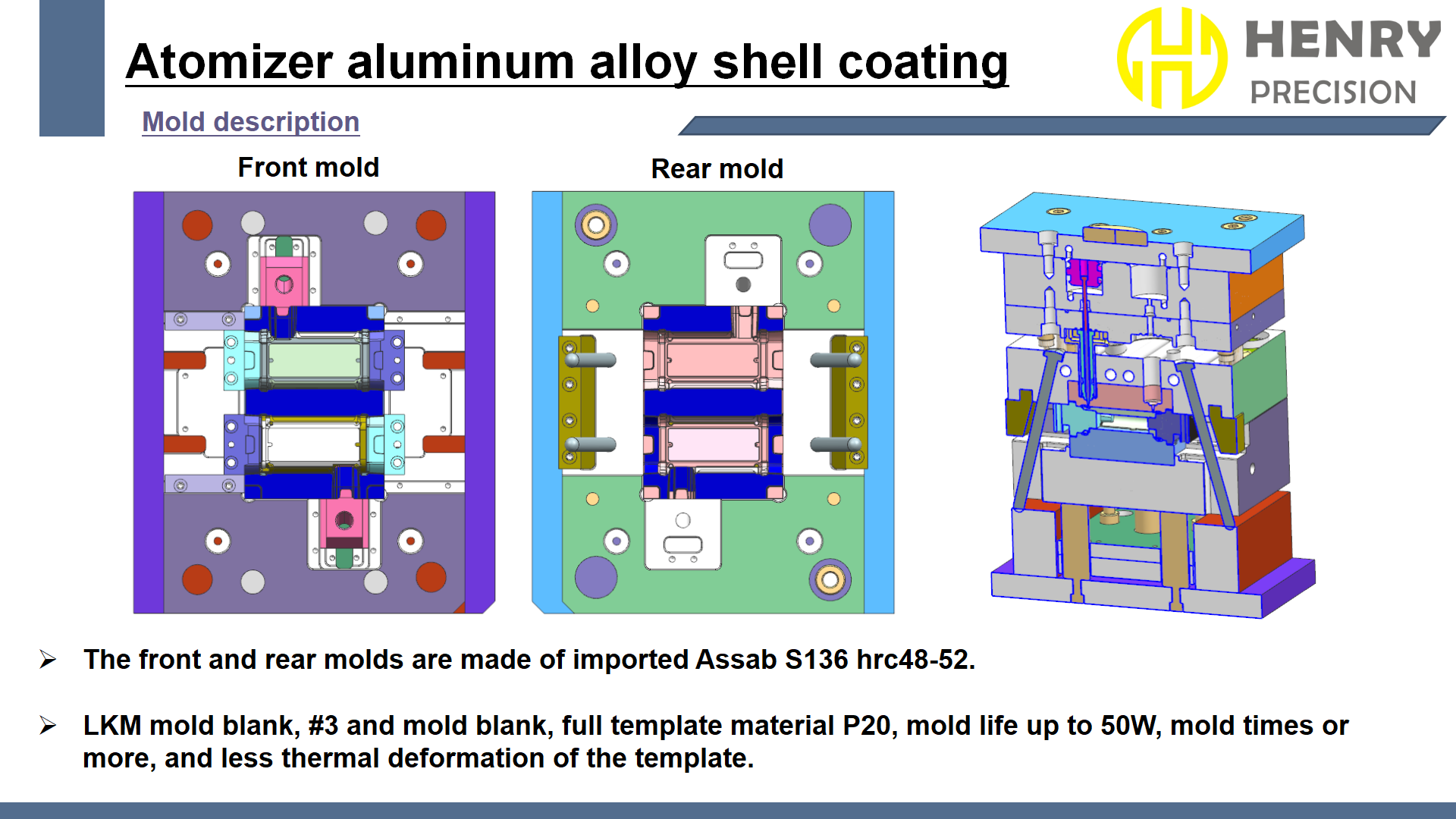
Mold Design and Material Selection
Assab S136 Steel for Front and Rear Molds
To ensure long-term durability and precision, we selected Assab S136 steel for the front and rear molds. This material has a hardness range of 48-52 HRC, making it resistant to wear and tear, ideal for high-precision injection molding applications.
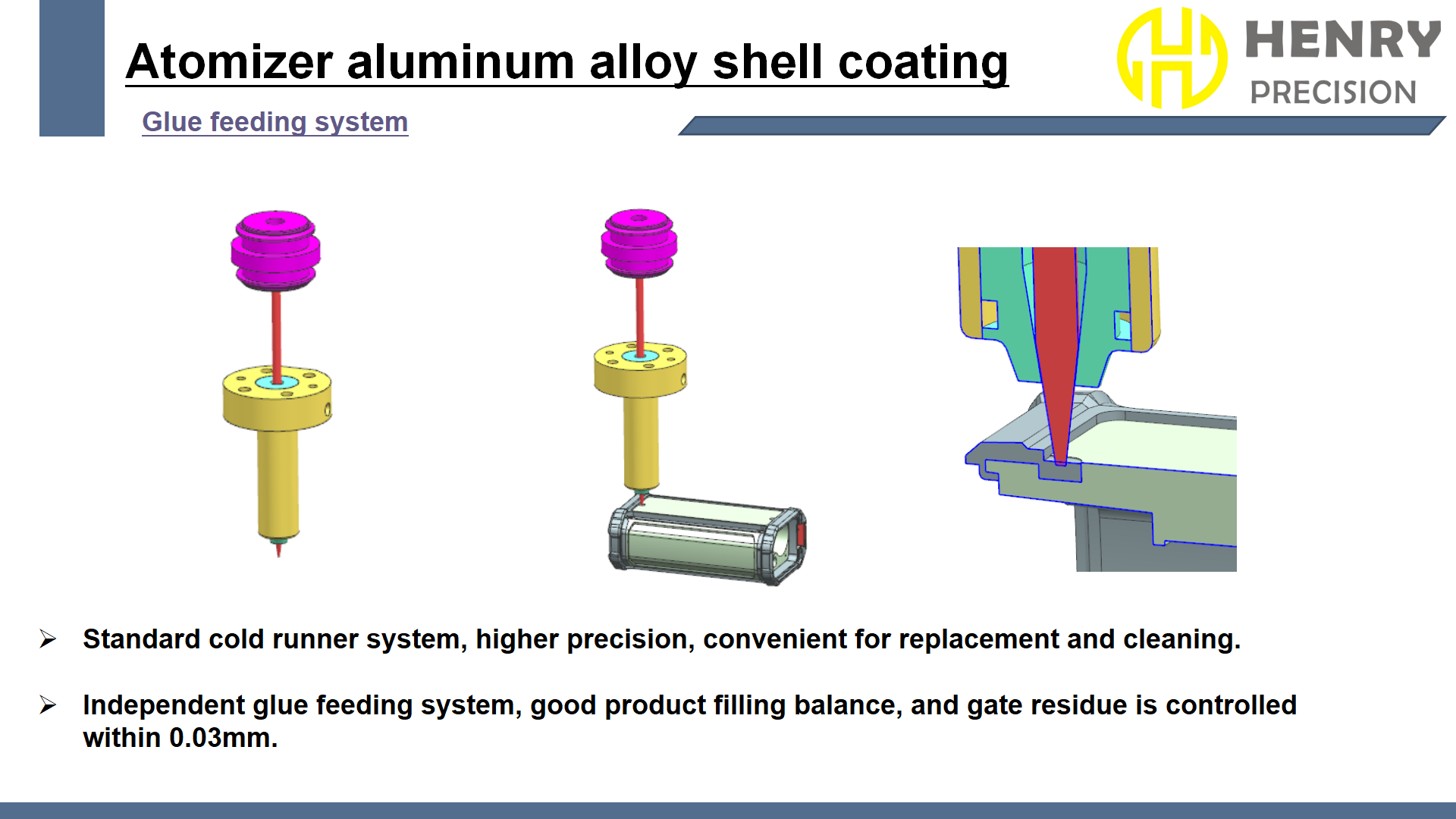
P20 Steel for Mold Blanks
The P20 steel used for the mold blanks provided easy machining and consistent molding performance. P20 is known for its high stability, making it an excellent choice for molds that require high-quality finishes and long production runs.
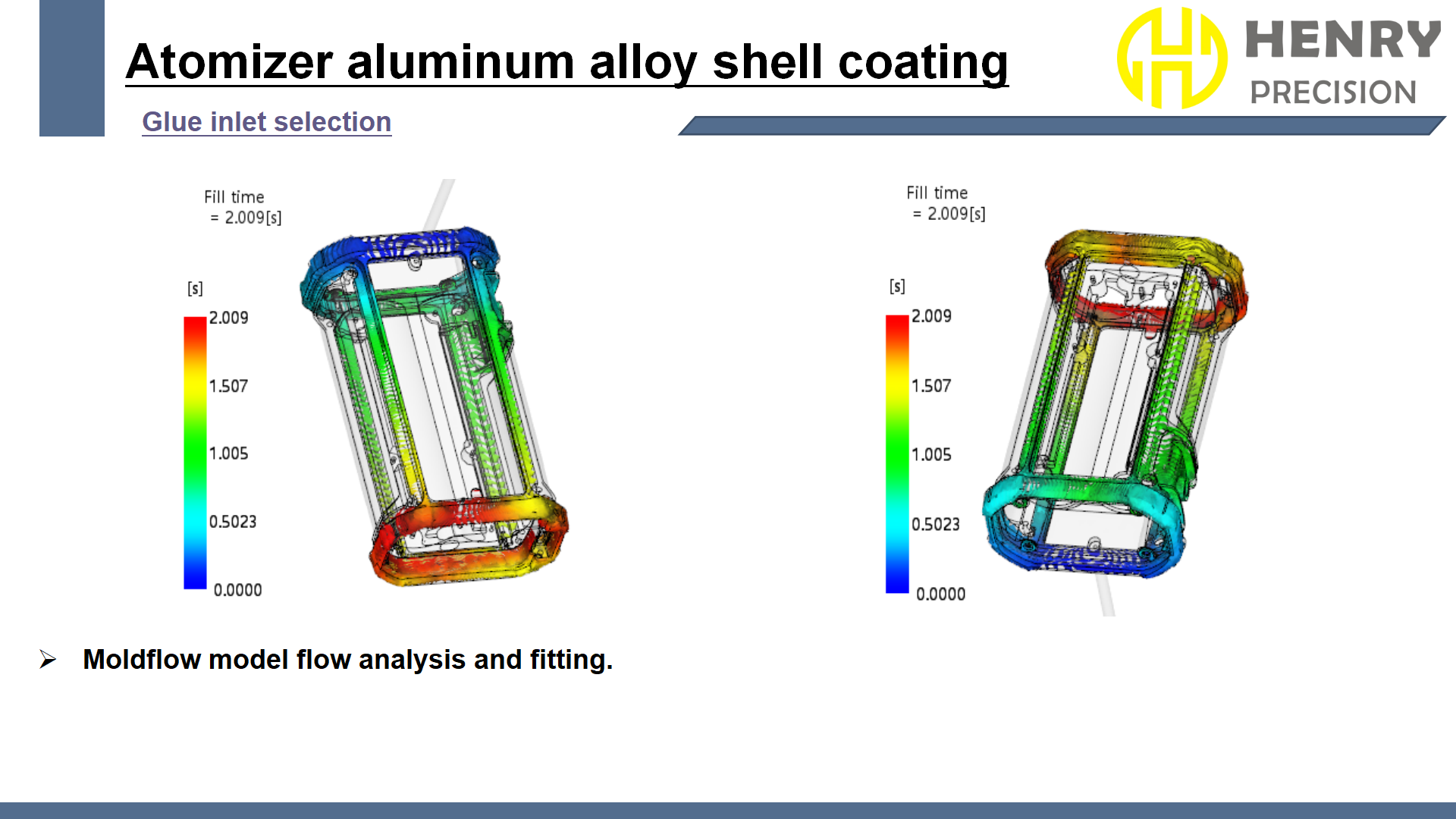
Liquid Silicone Rubber Wall Thickness and Flow Analysis
Optimizing Wall Thickness for Strength and Flexibility
One of the most critical aspects of the molding process was determining the wall thickness of the liquid silicone rubber (LSR). The ideal thickness was essential for balancing strength and flexibility. If the walls were too thin, the product would lack strength. If they were too thick, it would lead to material waste and longer cycle times.
We optimized the wall thickness through mold flow analysis, ensuring the material flowed evenly throughout the mold without issues.
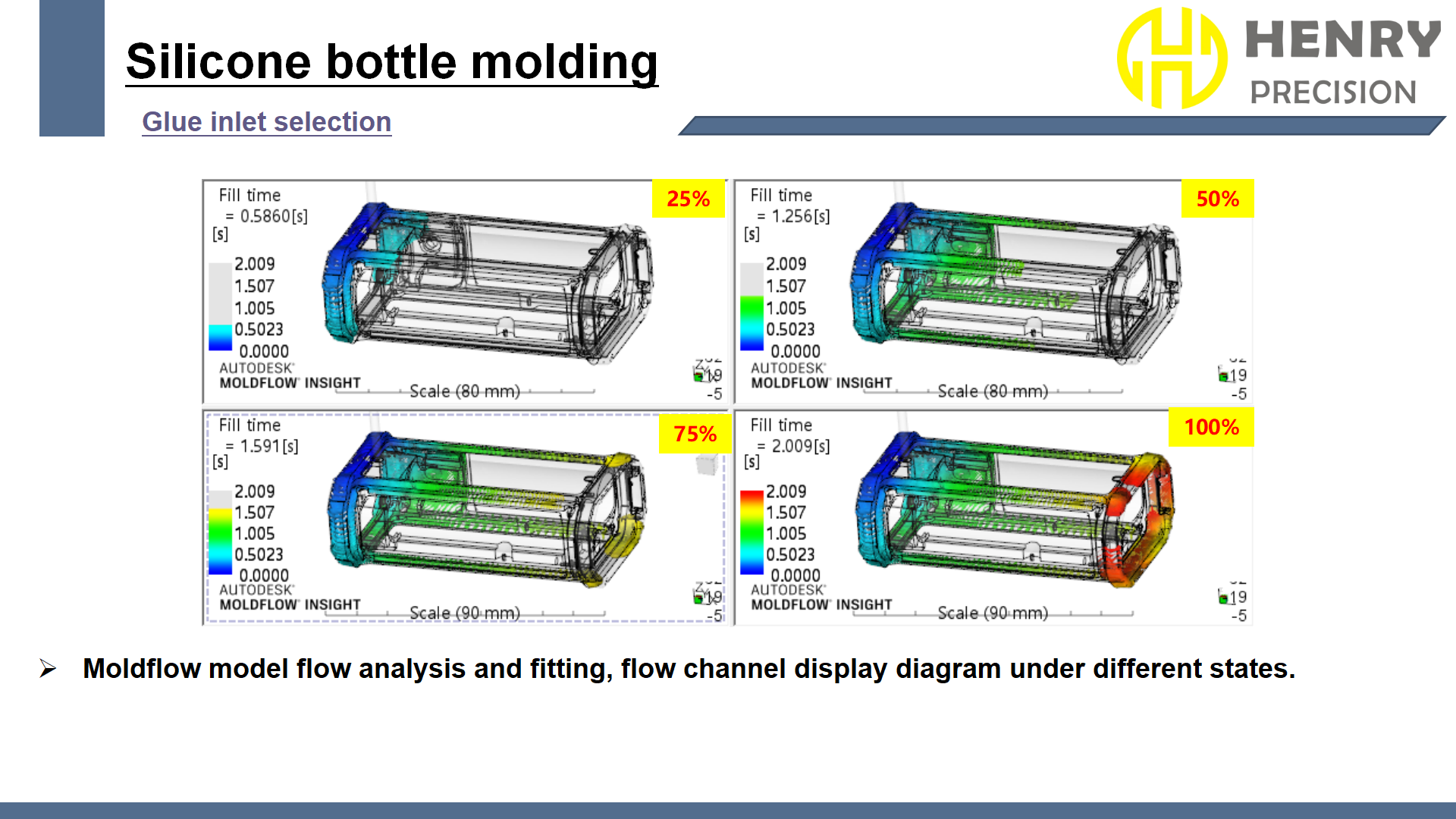
Using Mold Flow Simulation for Consistency
Using advanced mold flow analysis, we could simulate how the LSR would behave inside the mold during the injection process. This allowed us to adjust the molding parameters, ensuring that the silicone flowed consistently into all cavities and avoided defects like air traps or short shots.
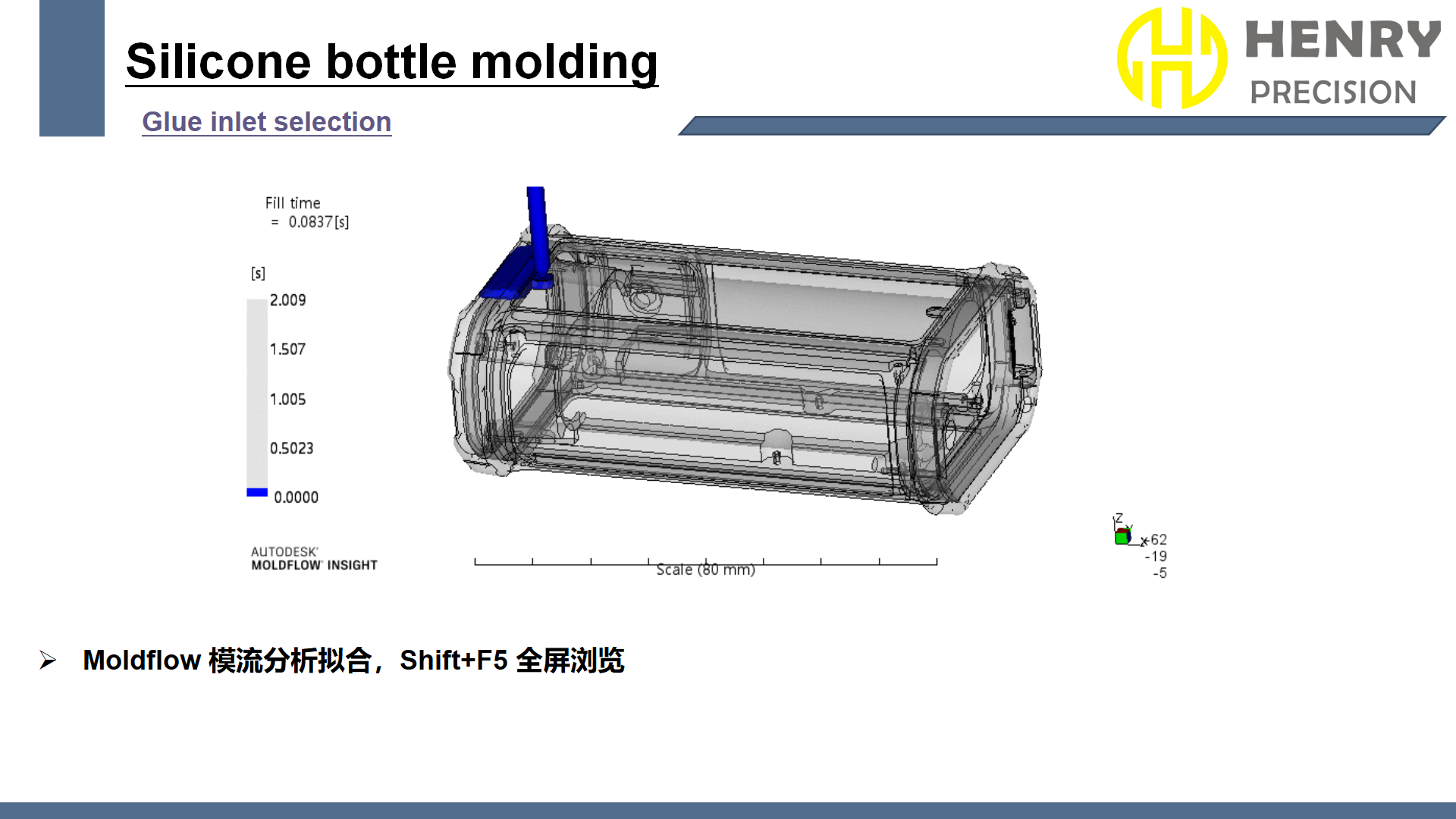
Quality Control and Mold Life
500,000 Cycle Mold Life
The choice of materials like Assab S136 steel and P20 steel ensured that the molds could withstand up to 500,000 cycles or more. This high mold life guarantees long-term production consistency, which is crucial for maintaining product quality over time.
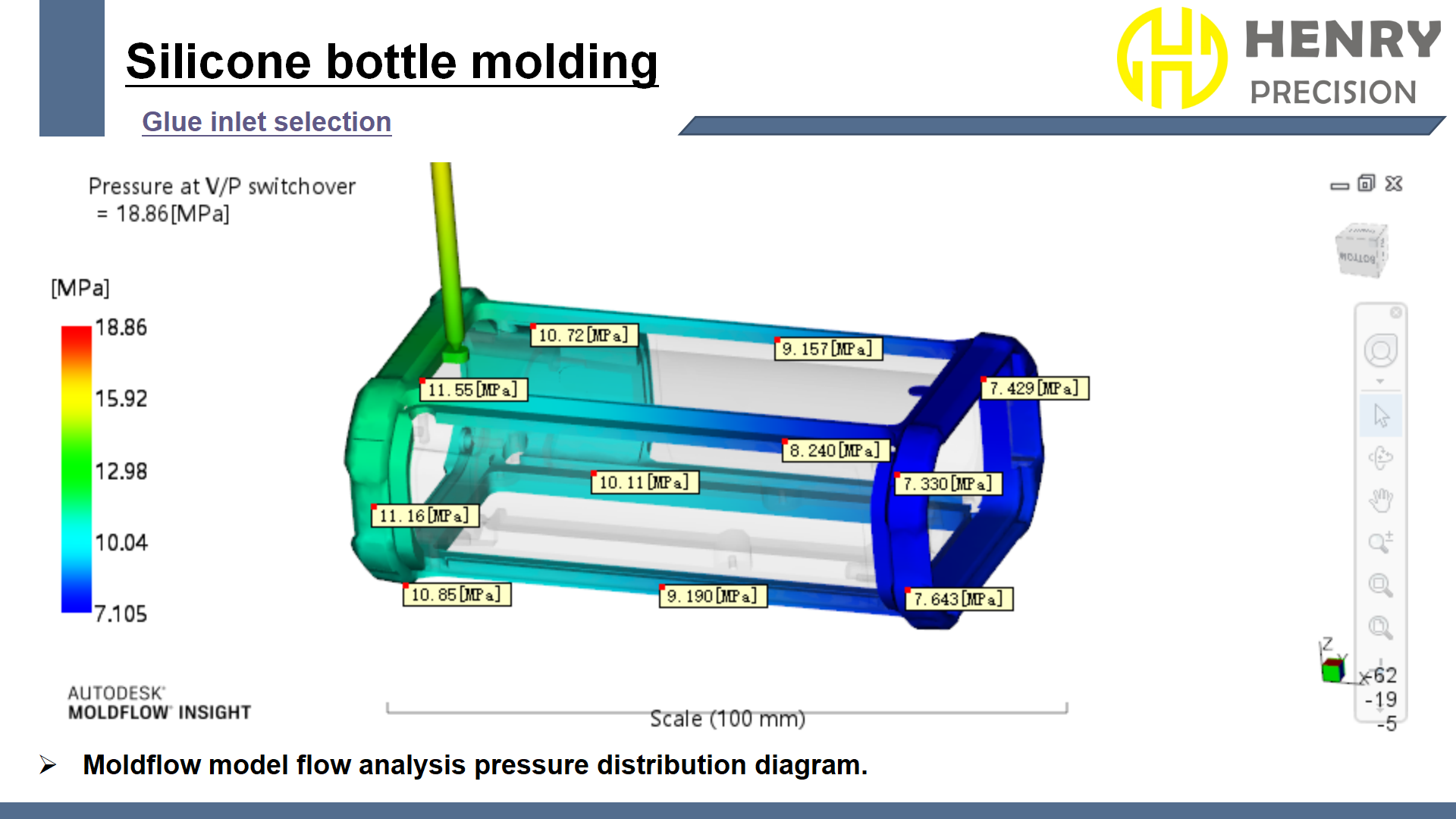
Quality Assurance with ISO Certifications
To ensure that every part met the highest standards, we implemented a rigorous quality control process. Our production follows ISO9001 and ISO13485 certifications, ensuring precision and reliability in every step of the production process.
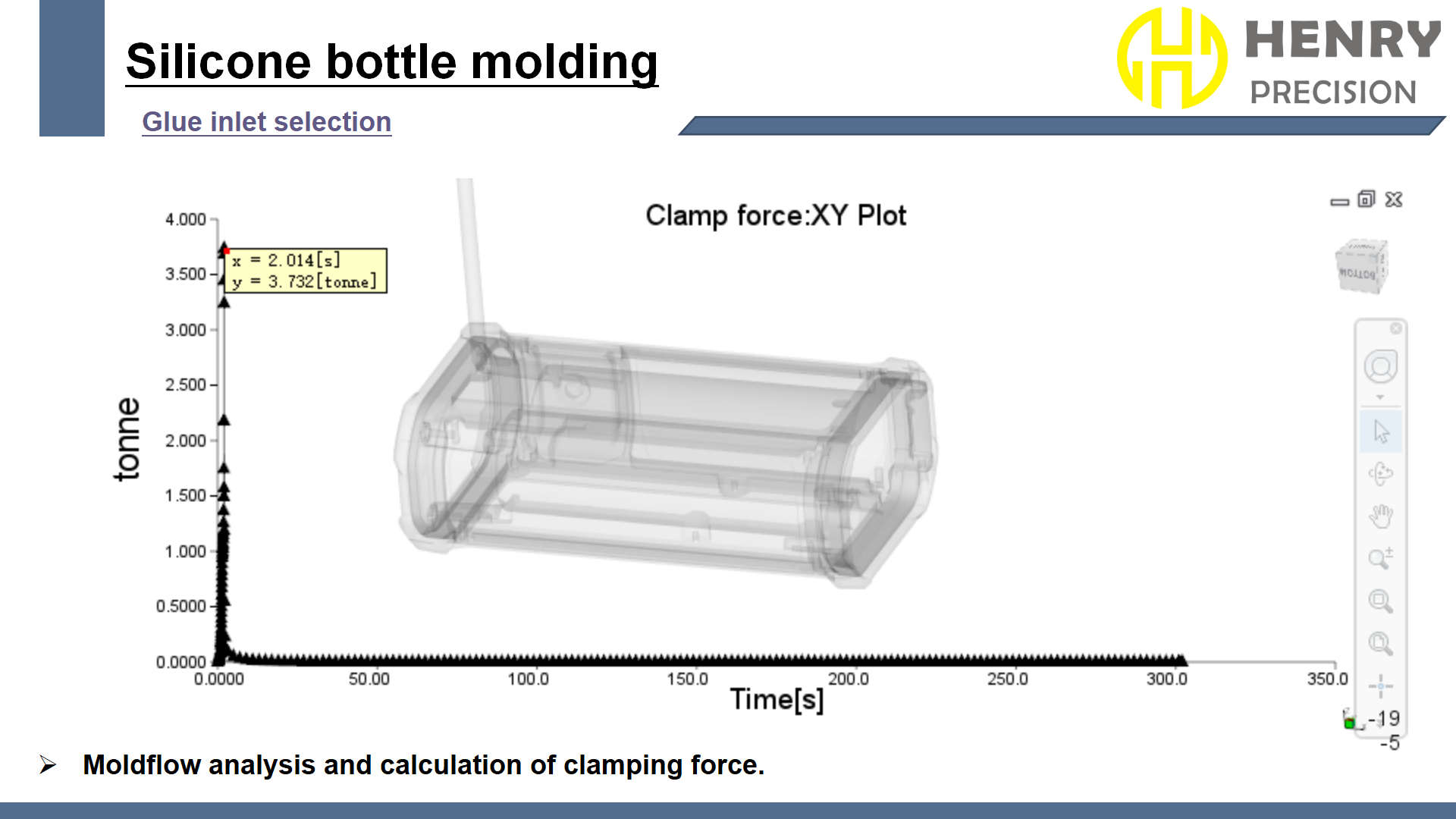
Efficient Production with Precision Mold Design
By integrating precision mold design and liquid silicone rubber injection molding, we successfully produced atomizer aluminum alloy shells that met all of our client’s requirements. The process, from wall thickness analysis to mold flow simulation, ensured that each product was manufactured with precision, efficiency, and quality.
The molds were durable, and the parts were consistent, which led to an overall successful outcome. If you are looking for reliable injection molding solutions or need help with custom mold design, our team is ready to assist you with your next project.
Contact Us for Customized Molding Solutions
Ready to bring your idea to life? Whether you need help with liquid silicone rubber molding, precision mold design, or custom manufacturing, we’re here to help. Contact Henry Precision today for a consultation and let us guide you through the process!