Analysis of Post-Processing Techniques for Plastic and Silicone
In industrial manufacturing, post-processing techniques for plastic and silicone play a crucial role in enhancing product appearance, performance, and durability. While both materials share some post-processing methods, their distinct properties lead to significant differences in processing techniques. This article explores the post-processing techniques for plastic and silicone to help businesses choose the right method for their applications.
1. Similarities in Post-Processing Techniques for Plastic and Silicone
1.1 Spraying
- Plastic: Used to enhance smoothness, wear resistance, or metallic texture. Common applications include UV protective coatings, rubberized paint, and glossy finishes.
- Silicone: Requires specialized silicone-compatible coatings to ensure adhesion while maintaining silicone’s flexibility.
1.2 Laser Engraving
- Plastic: Alters surface color through laser marking, providing high-contrast patterns suitable for logos, serial numbers, and other markings.
- Silicone: Suitable for transparent or semi-transparent silicone products without affecting material color, widely used in medical and consumer electronics fields.
1.3 Color Printing
- Plastic: Uses screen printing or pad printing, ideal for mass production with stable results.
- Silicone: Due to its low surface energy, plasma surface treatment is required before using specialized silicone inks for printing.
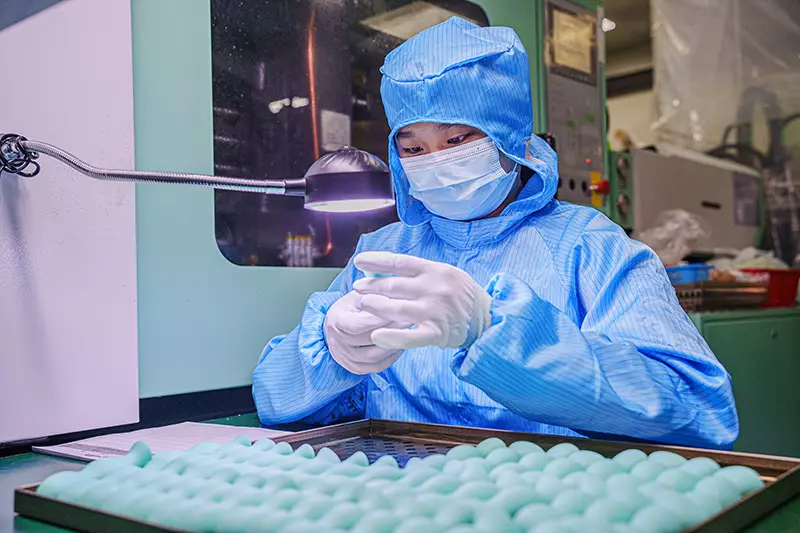
2. Exclusive Post-Processing Techniques for Plastic and Silicone
Technique | Plastic Products | Silicone Products |
---|---|---|
Electroplating | Supports chrome, nickel, and silver plating for enhanced texture and wear resistance. | Not applicable; does not support metal coatings. |
Thermal Transfer | Transfers patterns onto plastic using heat and pressure. | Difficult to adhere due to high heat resistance. |
Screen Printing | Standard inks can be used directly. | Requires plasma treatment to improve adhesion. |
Flocking | Uses adhesive to bond fibers, adding a soft texture. | Difficult to secure fibers due to high flexibility. |
Plasma Surface Treatment | Rarely used as plastics are generally compatible with most coatings. | Enhances surface energy, improving adhesion and printability. |
UV Protective Layer | Applied to outdoor plastic products to prevent aging and discoloration. | Prevents yellowing and aging of silicone, suitable for medical and food-grade products. |
Frosting | Achieves a matte texture through chemical etching or sandblasting. | Uses physical or chemical methods to enhance touch and premium feel. |
Hydraulic Pressing | Injection-molded plastic maintains its shape; rarely needed. | Commonly used for shape correction and dimensional accuracy. |
Polishing | Mechanical grinding to improve gloss and smoothness. | Used for minor defect removal but has limited impact on silicone. |
3. Recommendations for Choosing Post-Processing Methods
✅ Plastic Post-Processing: Focuses on decorative and wear-resistant properties, such as electroplating, thermal transfer, screen printing, and flocking, to enhance product aesthetics and market competitiveness. ✅ Silicone Post-Processing: Prioritizes functionality, including plasma treatment, UV protective layers, and hydraulic pressing, to improve durability, adhesion, and dimensional precision.
Businesses should select post-processing techniques based on application scenarios and performance requirements to enhance product quality and market appeal.
4. Conclusion
Post-processing techniques for plastic and silicone each have their own advantages. Companies should consider product characteristics, production costs, and application requirements when selecting the appropriate method. By making informed choices in post-processing, businesses can optimize product performance and increase market recognition.
📌 Recommended Resources:
We hope this article provides valuable insights into the post-processing techniques for plastic and silicone products!