📌 Project Overview
Industry: Daily Consumer Goods
Application: Leak-proof portable water cup
Material: Tritan™ Copolyester (BPA-free)
Process: High-precision injection molding + ultrasonic welding
🔍 Project Background
The client, a premium hydration brand from Europe, was developing a sleek, leak-proof, and eco-friendly water cup targeting the high-end retail market. The cup body required crystal-clear appearance, tight dimensional tolerance, and perfect sealing between the cup and the lid—posing significant challenges to injection molding quality and assembly.
⚠️ Technical Challenges
- Transparent Plastic Flow Marks
Transparent materials like Tritan™ are prone to flow lines, bubbles, and weld marks if not processed under optimal conditions. - Thread & Seal Precision
The thread area of the lid and the silicone seal groove required tolerances within ±0.05mm to ensure zero leakage. - Part Warpage Control
Asymmetrical part geometry increased the risk of shrinkage and warping during cooling. - Ultrasonic Welding Strength
Post-molding, the cup’s handle was assembled via ultrasonic welding—requiring precise welding lines to avoid weak bonding or deformation.
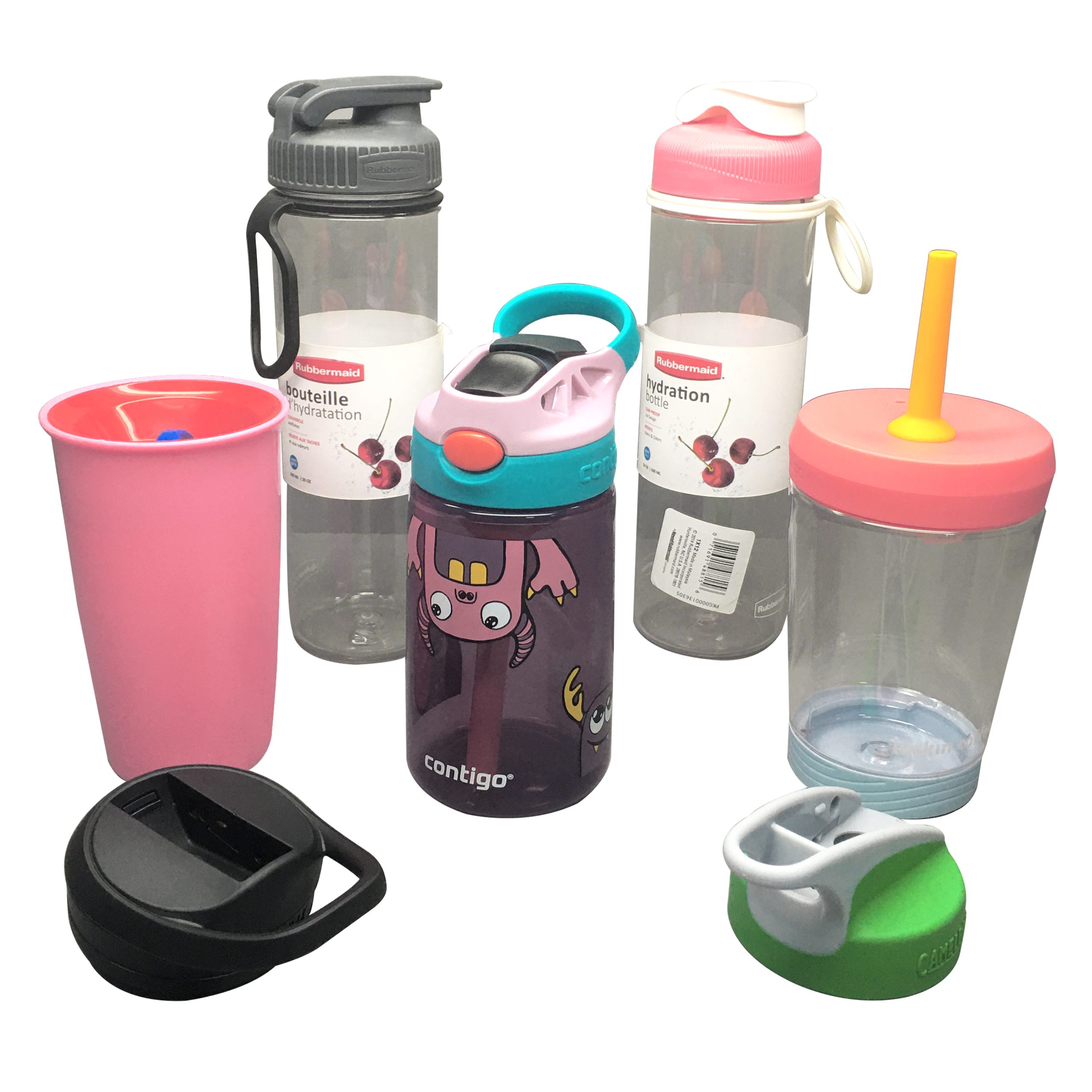
✅ Henry Precision’s Solutions
- Mold Flow Simulation
Comprehensive mold flow analysis was conducted to determine optimal gate location, minimize weld lines, and ensure uniform cooling. - Tooling Precision & Polishing
Mirror-polished steel cores and cavity inserts were used to deliver an optical-grade finish. Dimensional tolerances controlled within ±0.02mm. - Cooling System Optimization
Multi-zone waterway cooling channels helped balance shrinkage and reduce warpage in thin-wall sections. - Ultrasonic Welding Fine-Tuning
Our process engineers fine-tuned the amplitude, pressure, and time parameters, ensuring consistent strength and no flash at the joint. - Automated Inspection
Optical inspection systems were used to detect micro-defects such as bubbles, flow marks, and dimensional deviation before assembly.
🎉 Results
- Final product pass rate: 99.2%
- Visual appearance: Crystal-clear transparency with no flow lines
- Leak test: Passed 0.3MPa pressure water seal test with zero leakage
- Client Feedback: The client rated the quality and delivery consistency as “Excellent,” and has since expanded to multiple cup series using our molds and production services.
📦 Conclusion
With our advanced precision plastic molding capabilities, Henry Precision helped the client bring a premium, leak-proof hydration product to market—successfully combining aesthetics, function, and high-volume manufacturability.