Client Overview: Our client, a leading consumer electronics brand, required a rapid solution for the prototyping of a new product series. The challenge was to meet the tight timeline for product proofing and ensure that the prototypes matched the final design specifications, both in terms of appearance and functionality.
Challenge: The client required a high-precision prototype to showcase the design features of their new electronic device. They had a limited budget and a very tight deadline, needing the prototype to be produced in less than three weeks. The mold also needed to withstand up to 10,000 cycles of production.
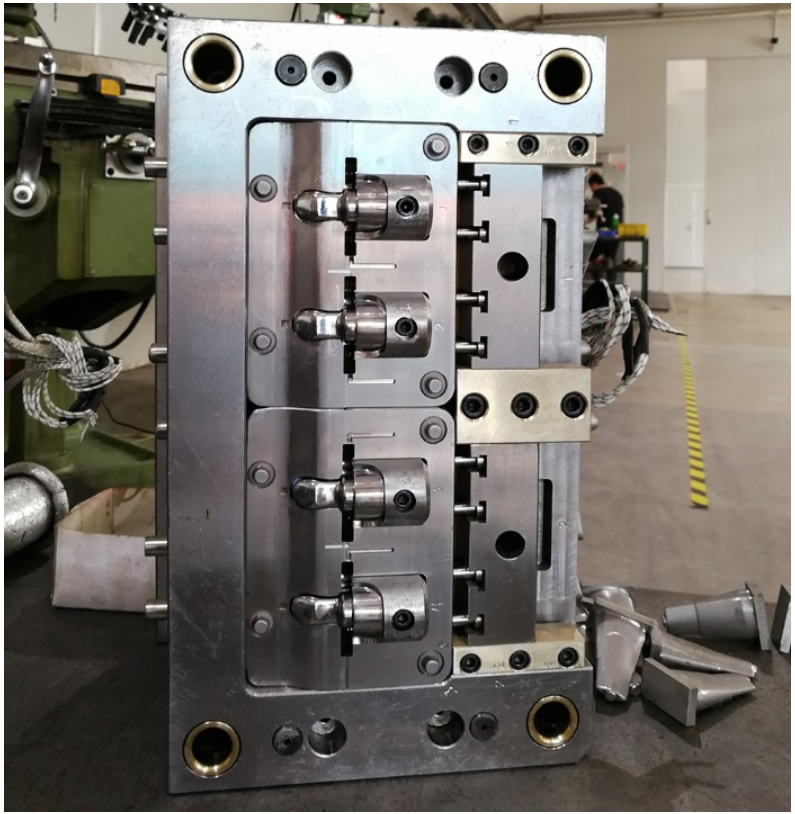
Solution: Henry Precision provided a rapid tooling solution tailored to the client’s needs. Here’s how we handled the project:
- Rapid Tooling Process:
- We selected S136h steel for the internal mold material, which is known for its excellent durability and high-quality finish. This material ensures that the molds can endure up to 10,000 production cycles without significant wear.
- The mold manufacturing cost was kept low, averaging between 5,000 to 10,000 RMB, helping the client stay within budget while ensuring the product met the highest quality standards.
- Quick Turnaround: The mold manufacturing time was optimized to just 1.5 to 2 weeks, allowing us to deliver the sample quickly.
- Flexibility in Engineering Changes:
- The client needed some last-minute adjustments to the design based on feedback from their internal testing. Rapid tooling provided the flexibility to make these changes quickly without compromising on quality.
- The product structure was modified and optimized as needed, ensuring that the prototype aligned with the final production requirements.
- Aesthetic Flexibility:
- The product’s appearance was not restricted by the tooling process. We were able to achieve both textured and highly polished surfaces on the prototype, meeting the client’s design specifications for visual appeal.
- Additionally, color restrictions were eliminated, allowing the client to choose the desired color for their prototypes.
- High-Quality Production:
- We ensured that the mold quality was reliable and that the prototypes were functionally equivalent to the final production parts.
- The service life of the mold was sufficient for the client’s needs, enabling smooth testing and validation during the product development phase.
Outcome: The rapid tooling process allowed Henry Precision to deliver high-quality, accurate prototypes within the client’s budget and tight deadline. The client was able to proceed with their product development without any delays, and the prototypes met both functional and aesthetic standards. They praised our ability to meet fast timelines and produce high-precision molds, and have since become a repeat customer for future projects.
Key Takeaways:
- Cost-Effective: Rapid tooling significantly reduces mold manufacturing costs while maintaining high precision.
- Fast Turnaround: Prototypes can be delivered in as little as 1.5 to 2 weeks, ideal for tight project timelines.
- Flexibility: Allows for easy adjustments to design and structure, ensuring prototypes match the final product specifications.
- Aesthetic Options: No limitations on surface texture or color, giving clients full control over the appearance of their prototypes.
If you’re looking for rapid tooling solutions to accelerate your product development, contact Henry Precision to learn more about how our services can help bring your ideas to life quickly and affordably.