As an important part of medical devices, the quality and precision of medical masks directly affect the safety and treatment effects of patients. There are many technical difficulties in producing medical masks. Especially in the injection molding process using liquid silicone rubber (LSR) and plastic materials, the product appearance, functionality and process control requirements are very high. This article will analyze several key difficulties and explore how to solve these problems through precise processes and equipment.
1. Appearance protection and physical damage control
Medical masks often need to meet high transparency requirements for easy observation and operation. However, transparent plastic parts are very susceptible to external physical damage during the production process, such as scratches, crushing or deformation. These damages not only affect the appearance of the product, but may also affect its performance and service life.
Solution:
In order to avoid appearance defects, protection must be strengthened during the production process during the picking, handling and assembly links, especially to avoid direct contact with sharp objects or heavy pressure. Automated picking devices and precision handling tools can be used to reduce the risks associated with manual operations. In addition, the design should consider the optimization of the mask structure as much as possible to reduce the vulnerable areas on the surface.
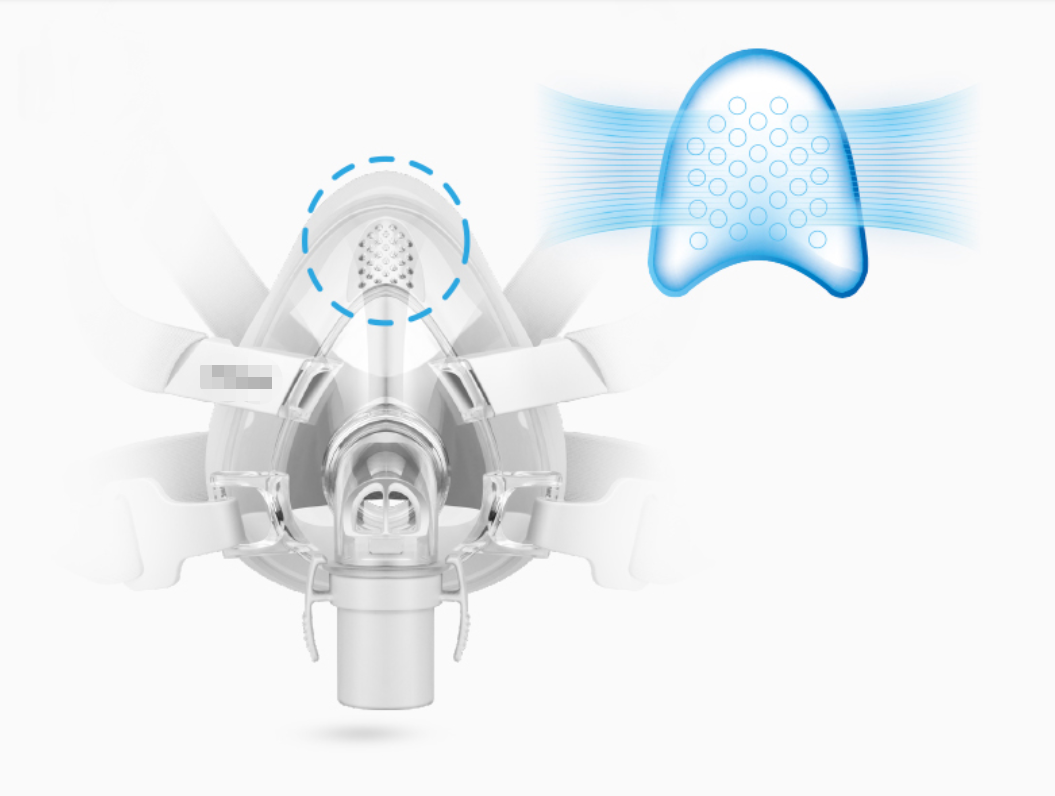
2. Problems in bonding corrugated silicone and plastic
In some medical mask designs, composite materials of corrugated silicone and plastic parts may be used to improve sealing, comfort and protection. However, the bonding of corrugated silicone to plastic often faces problems such as bubbles, debonding or poor adhesion. These defects can cause the mask to lose its seal during use, thus affecting its functionality.
Solution:
Solving this problem requires ensuring the stability of the molding equipment and precise process debugging. Especially in the process of bonding silicone to plastic parts, the molding temperature and pressure need to be controlled to ensure that the rubber can be evenly distributed and well bonded to the plastic surface. In addition, choosing the right bonding material and optimizing mold design are also key to avoiding such problems.
3. Temperature resistance and deformation control
Medical masks are often used in environments that involve high temperatures or prolonged wear. Therefore, the temperature resistance of the plastic part is particularly important. Once the temperature exceeds the tolerance range of plastic parts (usually 120°C), it may cause deformation, distortion or assembly tolerance violations of the plastic parts, ultimately affecting the comfort and sealing of the mask.
Solution:
For medical masks with higher temperature resistance requirements, materials with higher thermal stability, such as high-temperature plastics or composite materials, can be selected to improve the temperature resistance of the mask. During the production process, the mold processing accuracy and uniform temperature distribution need to be strictly controlled to ensure that each product can maintain a stable shape under temperature changes.
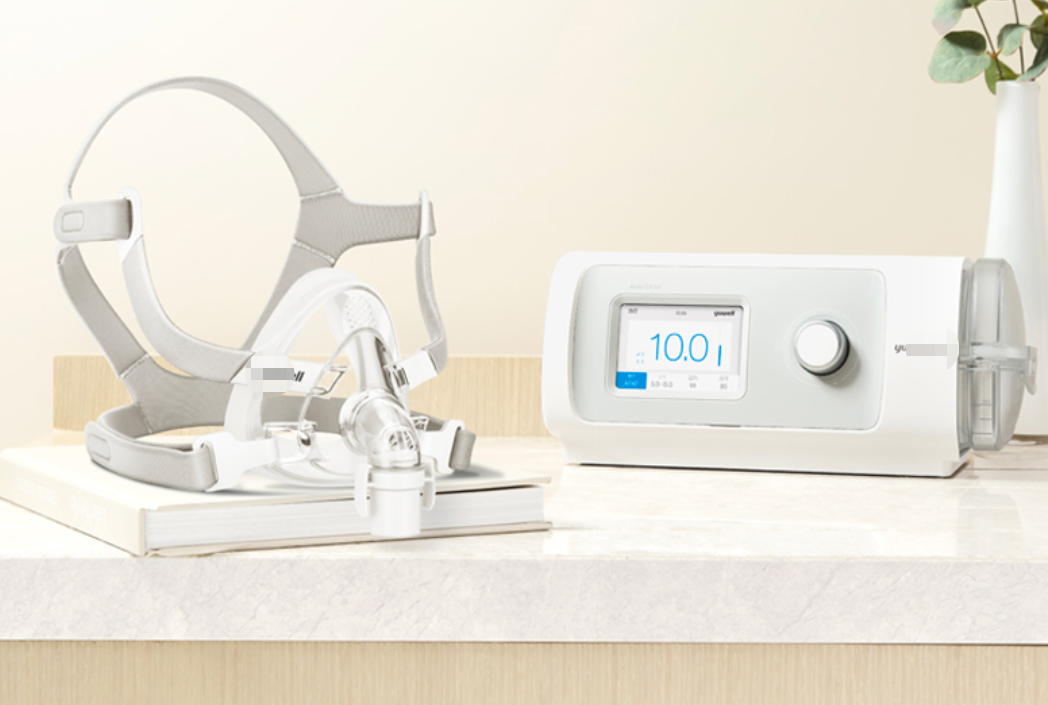
4. Silicone fluidity and appearance defects
Corrugated silicone has excellent fluidity, which is both an advantage and a challenge during the injection molding process. Due to its strong fluidity, it is easy to produce cloaks, bubbles or other appearance defects during the molding process. These defects not only affect the appearance of the mask, but may also affect its functionality, especially the effectiveness of the sealing part.
Solution:
In order to avoid defects such as cloaks caused by excessive fluidity, mold design needs to pay special attention to the optimization of flow channels to reduce excessive flow of materials. At the same time, the molding temperature, pressure, speed and other parameters can be adjusted to control the silicone flow process and avoid poor appearance.
5. Air outlet accuracy and gas flow
The air outlets in medical masks are usually designed with high precision, and their apertures and tolerances are strictly required. For example, the air outlet aperture is usually 0.8mm, the tolerance requirement is ±0.05mm, and it must meet specific air outlet volume standards. These requirements place high demands on the processing accuracy of the mold and the stability of the molding equipment.
Solution:
The key to solving this difficulty lies in the precision control of mold processing and the testing of gas circulation. During the production process, the mold design requirements must be strictly followed and high-precision processing must be performed to ensure the accuracy of the outlet size and position. In addition, the performance of the mask can be further verified through gas flow testing to ensure that it meets medical standards.
6. Challenges of forming concave structures
Some medical mask designs incorporate a concave structure to improve comfort and functionality. However, the molding of concave structures often faces greater technical challenges, including large undercuts and appearance texture defects (such as detachment, flower loss, and line loss). These defects can significantly affect the overall quality of the mask.
Solution:
For the production of concave structures, high-quality mold steel can be selected and its processing technology can be ensured to meet precision standards. At the same time, precise mold matching and temperature control systems should be used to avoid concave structural defects during the molding process. To this end, precise mold flow analysis and mold optimization design are essential.
7. Wall thickness control and molding difficulties
In the application of liquid silicone in some medical mask parts, the minimum wall thickness can reach 0.4mm, which places high demands on the molding process. Liquid silicone has strong fluidity, which can easily lead to defects such as air entrapment and glue deficiency, especially in parts with complex shapes.
Solution:
In order to avoid air entrapment and glue shortage problems, the injection process of liquid silicone needs to be carefully controlled to ensure that the performance of the molding equipment achieves a high degree of stability. Such defects can be effectively avoided by adjusting process parameters such as injection pressure, temperature and time.
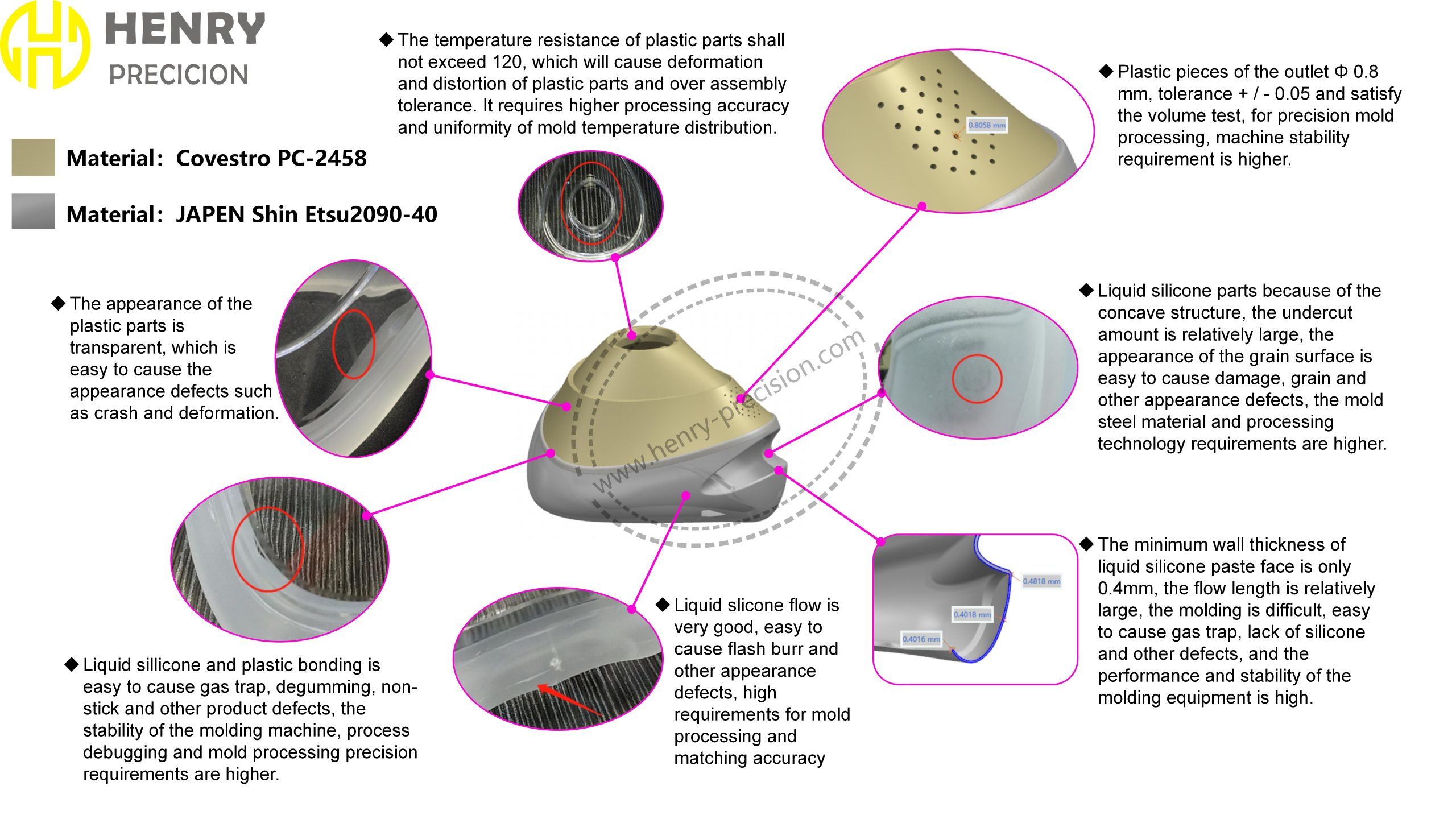
The production of medical masks is a complex process involving multiple materials and technical difficulties. From appearance protection, bonding problems, temperature resistance control to silicone fluidity, each link places strict requirements on equipment, molds and processes. In order to ensure product quality and performance, precise process design and high-standard quality control measures must be adopted to ensure that each medical mask meets the strict requirements of safety, hygiene and performance.