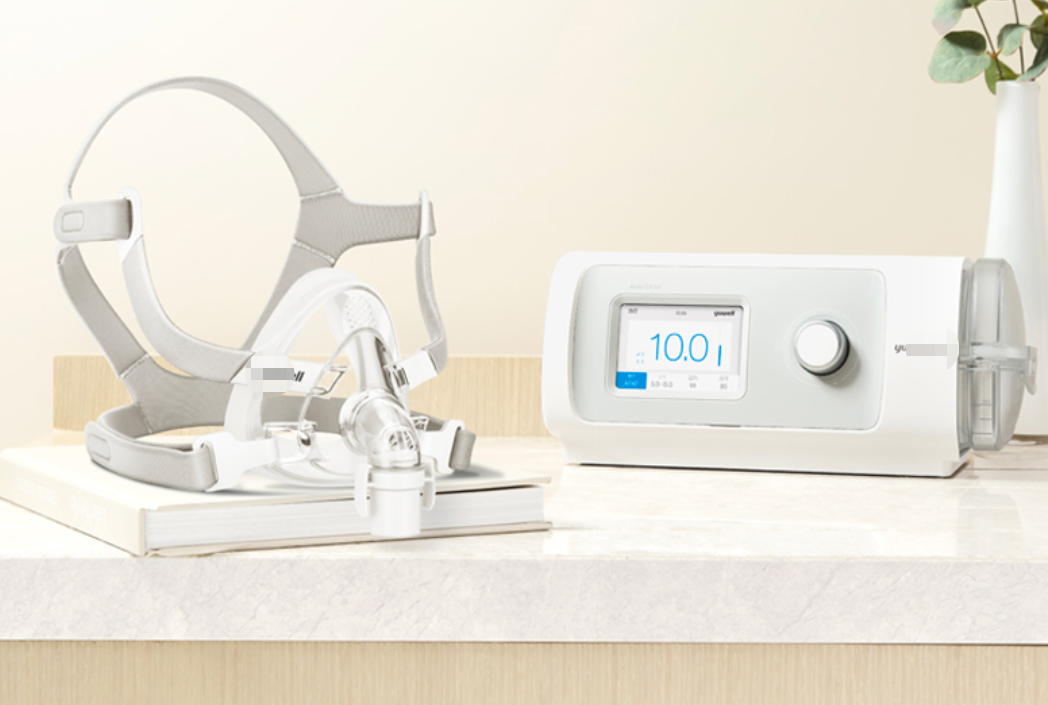
what is silicone Precision molding?
Henry Precision is a company that handles research, development, production, and sales of plastic molding. With a skilled design and technical team, we meet demanding requirements for high precision injection molding.
Our molds feature exceptional precision and smooth surfaces, earning global customer recognition for outstanding quality and performance.
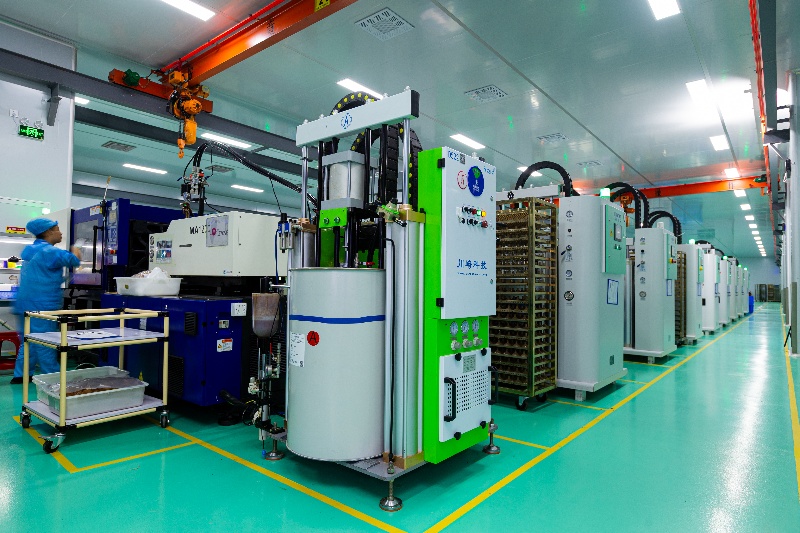
PRECISION PLASTIC MOLDING - EVERYTHING YOU NEED TO KNOW
What Is Precision Plastic Molding
Precision plastic injection molding is a highly accurate manufacturing process, ensuring dimensional tolerances within 0.01 mm, ideal for applications demanding exceptional precision.
Used widely in aerospace, automotive, precision instruments, sports equipment, and consumer products, it enhances reliability, functionality, and durability while minimizing material waste and costs.
At Henry, we achieve injection pressures over 25 MPa, speeds above 300 mm/s, and dimensional accuracy of 0.001 mm with a quality deviation rate under 0.1%.
We provide OEM plastic injection molding services. From prototype plastic injection molding to mass production, we excel in the this field, ensuring superior quality and reliability at every stage.
Applications of Precision Plastic Molding products
Precision injection molding is primarily used in aerospace, auto parts, precision instruments, sports equipment, testing tools, and other industrial & civil products.
Custom Plastic Injection Molding - Choose Henry as Your Trusted Partner
Industry-Specific Expertise
- Quality Control System: Strict protocols ensure products consistently meet high standards.
- Advanced Equipment: Our factories are equipped with cutting-edge tools, including high-end plastic injection machines, EDM, drilling, CNC machining, and milling devices.
- Precision Control: We accurately manage injection parameters, achieving dimensional accuracy of 0.001 mm and ensuring product stability. Our capabilities include handling injection pressure over 25 MPa and injection speeds of 300 mm/s or higher.
Advanced Innovative Ability
- Technical Strength and Innovation: Our skilled technical team excels in developing new technologies, products, and solutions.
- Mold Design Expertise: We specialize in designcomplex plastic injection molds to meet unique product requirements.
- Material Research: Our deep understanding of material performance helps optimize product quality.
Customer-Oriented Service
- Custom Solutions: Tailored injection molding services based on client requirements.
- Process Optimization: Continuous improvements reduce costs and enhance efficiency.
- Rapid Response: We quickly address customer needs with effective solutions.
High-Quality Materials Used in Plastic Injection Molding
We work with trusted partner suppliers for raw materials. If needed, we are happy to use materials provided by client-designated suppliers or the clients themselves, provided they align with the required standards.
polypropylene (PP) | good chemical resistance, heat resistance and electrical insulation, relatively low cost, commonly used in automotive parts, daily necessities. |
polycarbonate (PC) | high strength, good transparency, excellent heat resistance, commonly used in electronic appliances, optical instruments, building materials, etc.. |
polystyrene (PS) | good insulation and processing performance, commonly used in electronic product shells, toys and so on. |
acrylonitrile-butadiene-styrene copolymer (ABS) | good overall performance, with high strength, toughness and surface gloss, widely used in home appliances, automobiles, electronics and other fields. |
Polyamide (PA, nylon) | high abrasion resistance and mechanical strength, commonly used in gears, bearings, automotive parts and so on. |
polyformaldehyde (POM) | excellent mechanical properties, wear resistance and self-lubricating, commonly used in precision machinery parts, automotive parts, etc.. |
polymethyl methacrylate (PMMA, acrylic) | extremely high transparency, good optical properties, commonly used in lighting fixtures, optical instruments. |
polyethylene (PE) | including high-density polyethylene (HDPE) and low-density polyethylene (LDPE), with good corrosion resistance and insulation, commonly used in packaging materials, pipelines and so on. |
polyvinyl chloride (PVC) | good chemical resistance, low price, commonly used in building materials, pipelines, etc.. |
thermoplastic polyester (PBT) | good heat resistance, moisture resistance and electrical properties, commonly used in electronic and electrical appliances, automotive parts and so on. Each of these materials has its own characteristics and scope of application in precision plastic molding, the specific choice of which material depends on the product performance requirements, cost budget and production process and other factors. |
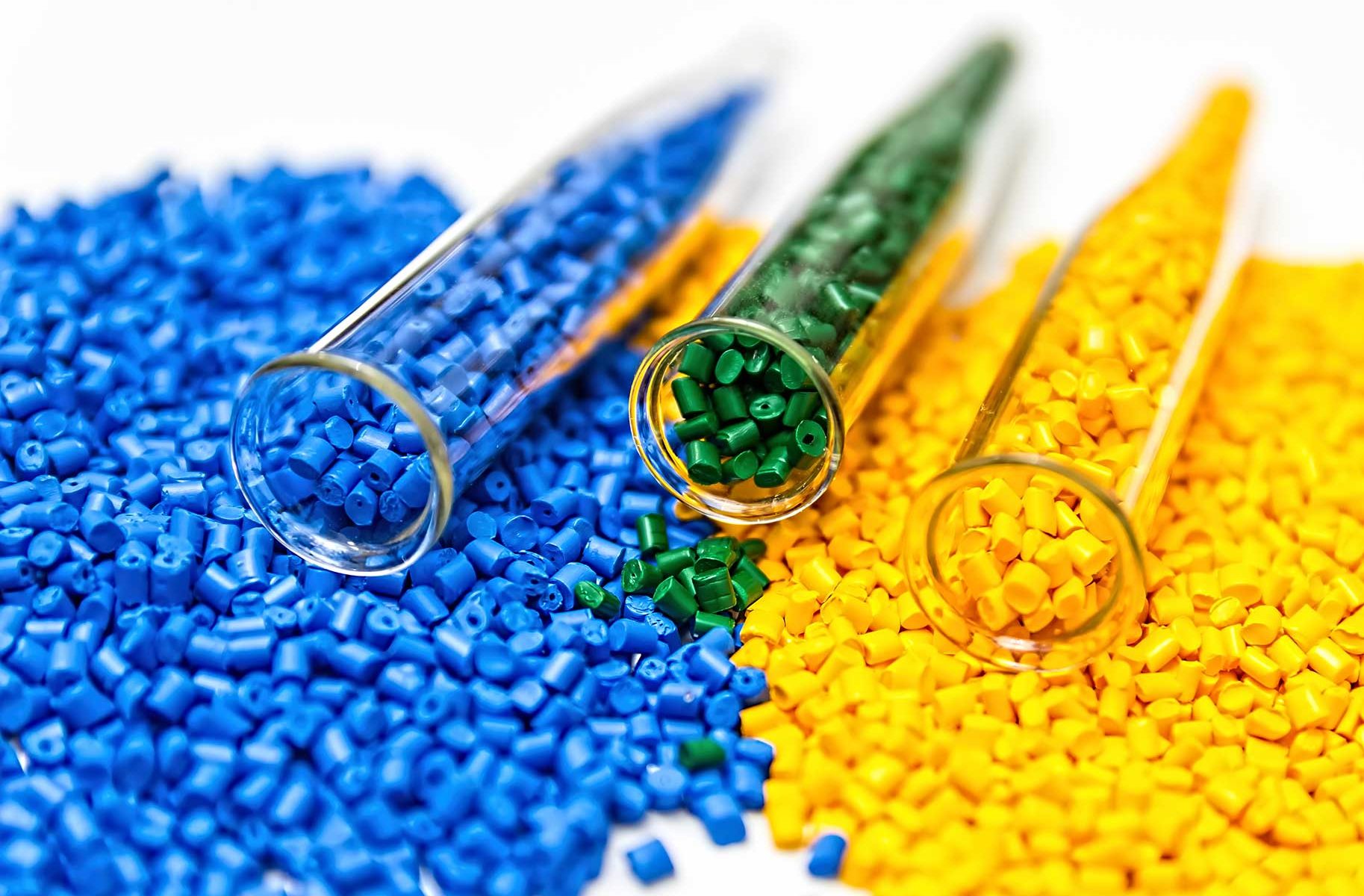
Cases
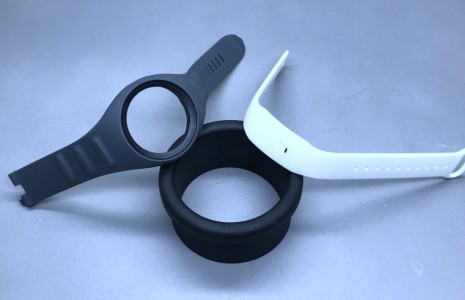
This is an editable piece of text,This is an editable piece of text,This is an editable piece of text,
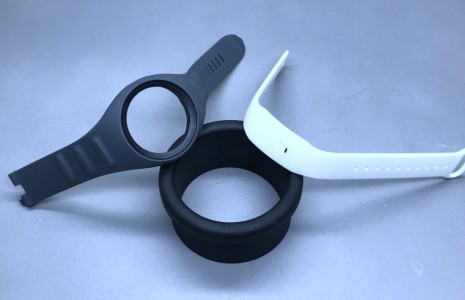
This is an editable piece of text,This is an editable piece of text,This is an editable piece of text,
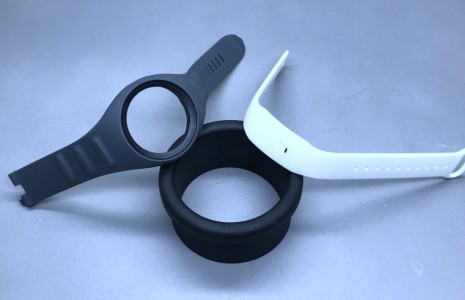
This is an editable piece of text,This is an editable piece of text,This is an editable piece of text,
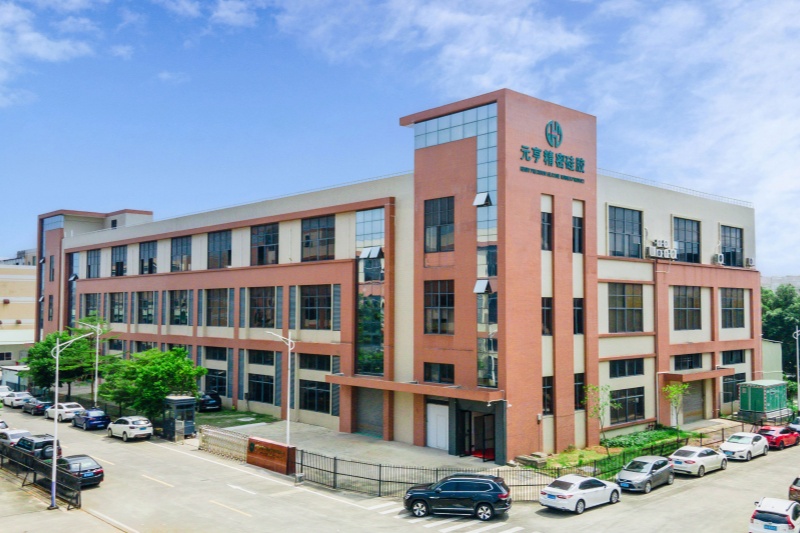
Partner with Henry-precision to Experience:
Premium Precision Plastic Excellence
- Advanced in-house tooling for precise plastic injection moldedcomponents
- Flash-free production with minimal waste
- Streamlined manufacturing requiring no post-processing
- Specialized cold runner systems for optimal material control
Advanced Manufacturing Capabilities
- State-of-the-art automated production facilities
- High-precision injection molding systems
- Integrated quality control processes
- Industry-leading 6Smanagement implementation
Expert Technical Support
- In-house mold design and fabrication expertise
- 30+specialized technical professionals
- Customized R&D solutions
Comprehensive project support from concept to production
Cooperation Process

Request a Quotation
Upload your 2D/3D files and product details. Our team will review the submission and provide an accurate quotation within 24 hours, ensuring a quick and efficient start to your project.

Confirm the order
Upon confirming the purchase order, we deliver a detailed Manufacturing Analysis Report. This report reviews tolerances, cosmetic specifications, and identifies any potential quality-impacting issues for your approval.

DFM Review
Collaborating with you, we refine mold flow analysis, dimensions, tolerances, and appearance specs. Your timely approval of Design for Manufacturing (DFM) Review ensures optimized production planning.

Production & Quality Assurance
With DFM approval, our dedicated project engineers oversee the entire production process. Inspections are performed under ISO9001 and ISO13485 standards to ensure precision and consistency.

Timely Delivery & After-Sales Support
After quality assurance checks, parts are packaged and delivered promptly. Our team remains available to address any post-delivery concerns, ensuring your complete satisfaction.
Let’s build the future with innovation.
Please provide the following details to help us better understand your needs and get in touch with you as soon as possible.
You can send us 3D drawings in STL, STEP, IGES and 2D drawings in PDF. We will provide accurate quotations within 24 hours.
From concept to completion, we provide a one-stop silicone mold manufacturing service.