Post Processing Service
The post-processing of plastic and silicone products, crucial in manufacturing, aims to enhance the appearance and performance of finished goods. These treatments boost a product’s competitiveness in the market and broaden its application range.
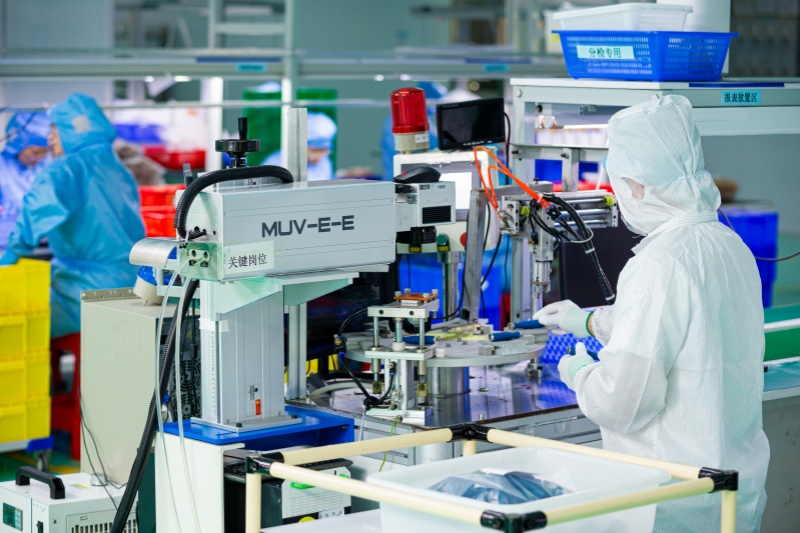
1.Post-treatment of plastic products
- Spray: By coating the plastic surface with a layer of paint, and then use high temperature baking to make the paint curing. This method can improve the aesthetics of the product, adding color and texture, but also provides a certain protective layer to prevent scratching and corrosion.
- Electroplating: Electroplating can cover the surface of plastic products with a metal film, which not only improves aesthetics, but also enhances abrasion and corrosion resistance. Commonly used plating materials include chrome, nickel or silver.
- Sanding and Polishing: The surface of a plastic product is treated with sandpaper, a grinder, or a polisher to remove burrs and unevenness and give the product a smoother, brighter surface.
- Screen Printing: Printing text or patterns on the surface of the product through screen printing technology, often used for product identification, decoration or instructions to convey information.
- Thermal transfer: The use of special transfer paper or film, through the way of hot pressure to transfer the pattern to the plastic surface, suitable for complex patterns of accurate reproduction.
- Spraying: Spraying is often used to add beauty and durability to a product. Different coatings can be selected to achieve the desired effect, such as matte, glossy or metallic effects.
- Laser engraving: The use of laser technology to make fine engravings on products, suitable for creating fine markings or complex patterns.
- Flocking: Coated with special glue on the plastic surface, then the fluff adhered to it, fixed after drying, so that the surface of the product shows a soft texture, commonly used in toys and decorative items.
2.post-processing of silicone products
- Spraying: Similar to the spraying of plastic products, silicone products can also be sprayed to change the color or add special effects, such as matte or UV coating.
- plasma surface treatment: through plasma treatment technology to change the chemical composition of the surface of the silicone, to improve its bonding ability, to facilitate the subsequent bonding or printing process. 3. laser engraving: the same as the plastic products to change the color and add special effects, such as matte or UV coating.
- Laser engraving: Similar to laser engraving, but especially suitable for transparent or semi-transparent silicone materials, it can create delicate logos or patterns without affecting the color of the material itself.
- UV protective layer: Coating a layer of UV protective layer on the surface of silicone products can effectively prevent aging and yellowing caused by ultraviolet radiation.
- Color Printing: Direct color printing on silicone products to add design patterns or brand logos to increase visual appeal.
- Frosting: Through physical or chemical methods to make the surface of silicone products show frosted effect, to increase the sense of touch and beauty of the product.
- Hydraulic Pressing: Using hydraulic presses to correct the shape and perfect the details of the silicone products to ensure the dimensional accuracy and appearance quality of the products.
- Polishing: Mechanical polishing of silicone products by soft cloth wheel and other tools to enhance the luster and smoothness of the surface.
Post-processing method-01
Process and procedure
– Cleaning: First of all, use anhydrous alcohol or special cleaner to thoroughly clean the TPU + ABS material face massager, remove the surface of dust, grease and other pollutants. Sanding: If there are slight defects or unevenness on the surface, use fine sanding.
– Sanding: If there are slight imperfections or unevenness on the surface, use fine sandpaper to gently sand it, and then clean it again.
– Use masking tape and plastic film to cover the parts of the massager that do not need to be painted, such as electronic components, ports and so on.
– Paint selection: choose the paint suitable for TPU+ABS material, generally recommended to use flexible and strong adhesion of polyurethane or acrylic paint.
– Color Blending: Blend the required color according to the product design requirements.
– Choose the primer suitable for TPU+ABS material and mix it according to the paint instruction.
– Spraying method: Use air spray gun or automatic sprayer to operate, keep the distance between the spray gun and the object to be sprayed is about 20-30cm, move the spray gun evenly to avoid uneven coating.
– Wait for the primer to dry, usually a few hours to a day, depending on the ambient temperature and the type of primer.
– Mix the topcoat in the desired color.
– Apply the topcoat using the same spraying method as for the primer. Apply as many coats as necessary, allowing appropriate drying time between coats.
– Pre-bake: Pre-bake at a lower temperature (approx. 50°C-60°C) for approx. 15-30 minutes to allow most of the solvents to evaporate.
– High temperature baking: then baking at higher temperatures (approx. 70°C-80°C) for a period of time generally ranging from 30 minutes to 1 hour to ensure that the coating is fully cured.
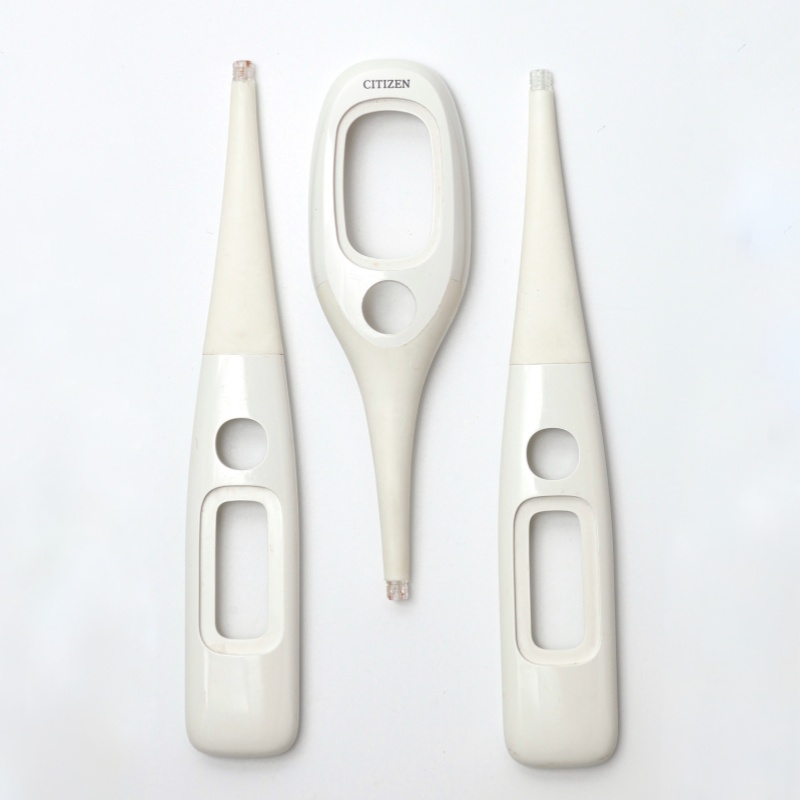
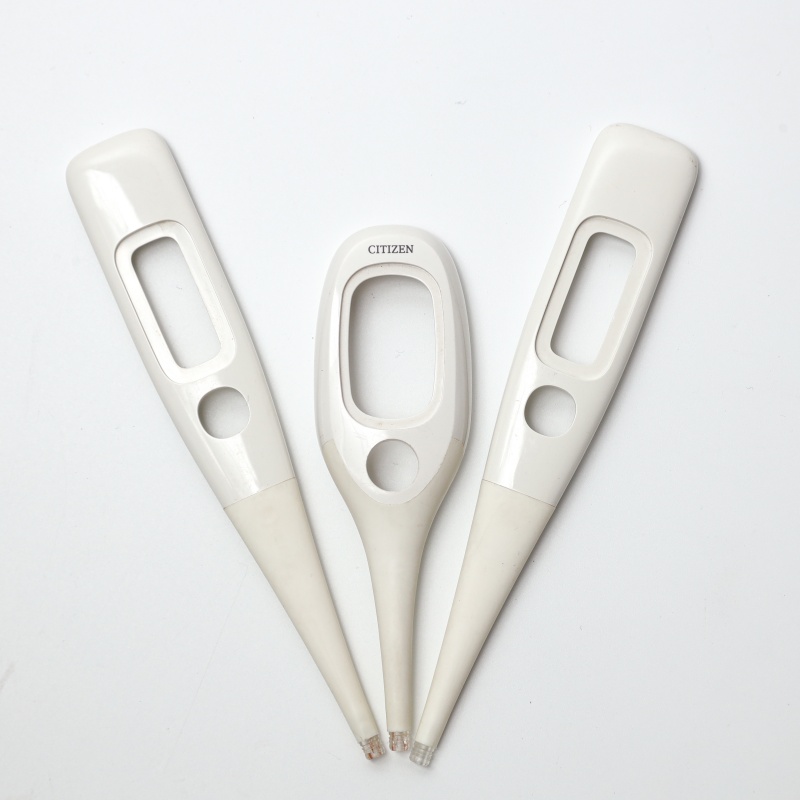
Post-processing method-02
In the medical products industry, the manufacture of respiratory masks involves strict standards and protocols, especially for products used in clinical environments. The products are usually made of PC material combined with liquid silicone through a mold overmolding process to ensure transparency, durability and comfort. The following is a detailed introduction to the post-treatment process of the silicone part of the respiratory mask – UV light treatment process, the required equipment, precautions and product maintenance methods.
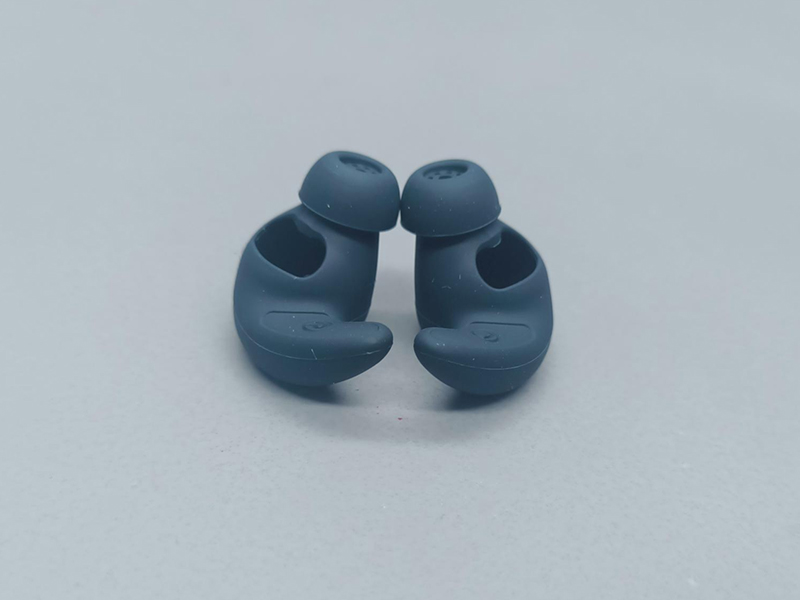
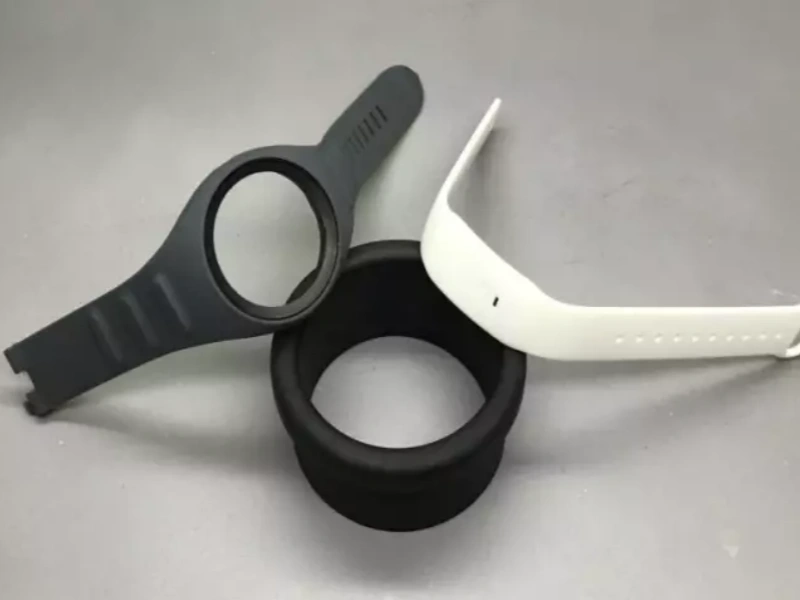
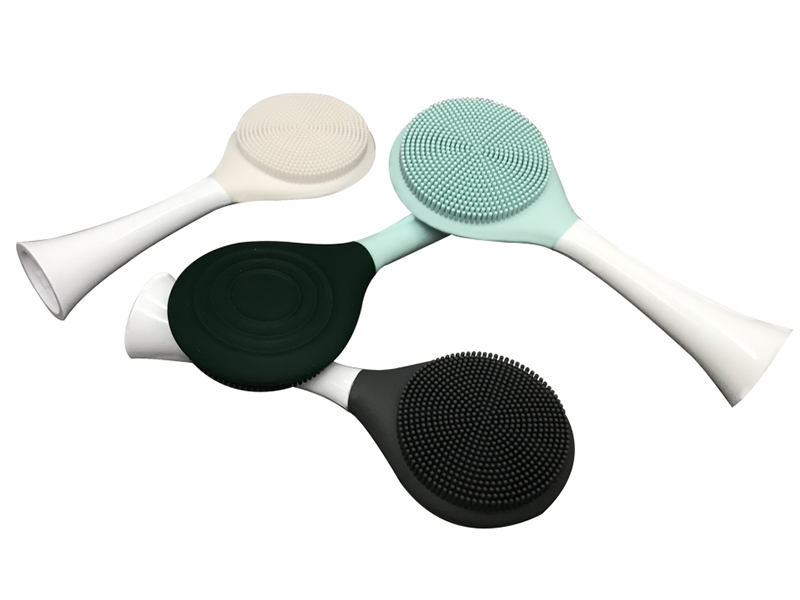
UV light treatment process
– Cleaning: first of all, thoroughly clean the molded silicone part, use anhydrous alcohol or medical grade cleaner to remove all pollutants on the surface.
– Inspection: Preliminary inspection of the cleaned silicone to ensure that there are no physical defects such as bubbles, cracks, etc..
– Equipment preparation: prepare UV light irradiation equipment to ensure that its function is normal, the intensity of the light source meets the requirements.
– Irradiation: put the silicone parts under UV light irradiation, the time is adjusted according to the type and thickness of the silicone, generally a few minutes to ten minutes. UV light irradiation can make the surface of the silicone to produce a smooth effect, reduce friction, and improve the wearing comfort.
– Re-cleaning: After the UV treatment, the silicone parts are cleaned again with a medical grade cleaner to remove any residue that may have been generated by the treatment process.
– Final Inspection: Conduct final quality inspection, including visual inspection and hand feeling inspection, to ensure that the treated silicone surface is smooth and free from defects.
Let’s build the future with innovation.
Please provide the following details to help us better understand your needs and get in touch with you as soon as possible.
You can send us 3D drawings in STL, STEP, IGES and 2D drawings in PDF. We will provide accurate quotations within 24 hours.
From concept to completion, we provide a one-stop silicone mold manufacturing service.